2018 ACADIA Project
Summer 2018 | Iowa State University | College of Design
WAFT is an interdisciplinary collaboration between researchers in architecture, computation, and ceramics. The project integrates traditional slump molding techniques and handmade glazes with computationally designed and 3D printed ceramic tiles and CNC milled molds. WAFT is the result of an ongoing partnership at the Iowa State University (ISU) Computation + Construction Lab (CCL) between the departments of Architecture and Arts & Visual Culture at ISU’s College of Design. The project relies upon digitally assisted fabrication: the combination of manual and digital fabrication practices. WAFT leverages both ceramic knowledge and digital fabrication capabilities to create designs that neither discipline could produce in isolation.
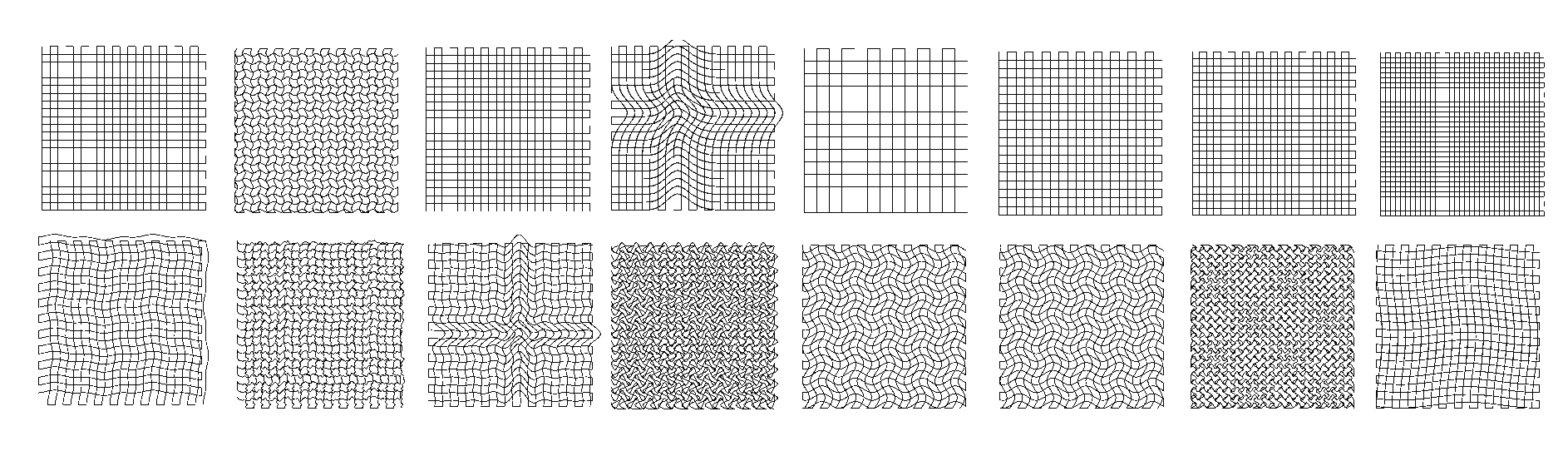
The tiles were designed using grasshopper allowing rapid customization of the pattern, gradient and density. Layers were printed in pairs of 2, 4, or 6 creating a weave there the structure of the tile is strengthened through the overlap of the clay between layers. Tiles size remained consistent at 6” (X) x 6” (Y) and layer height for the clay remained constant at 2.8 mm.
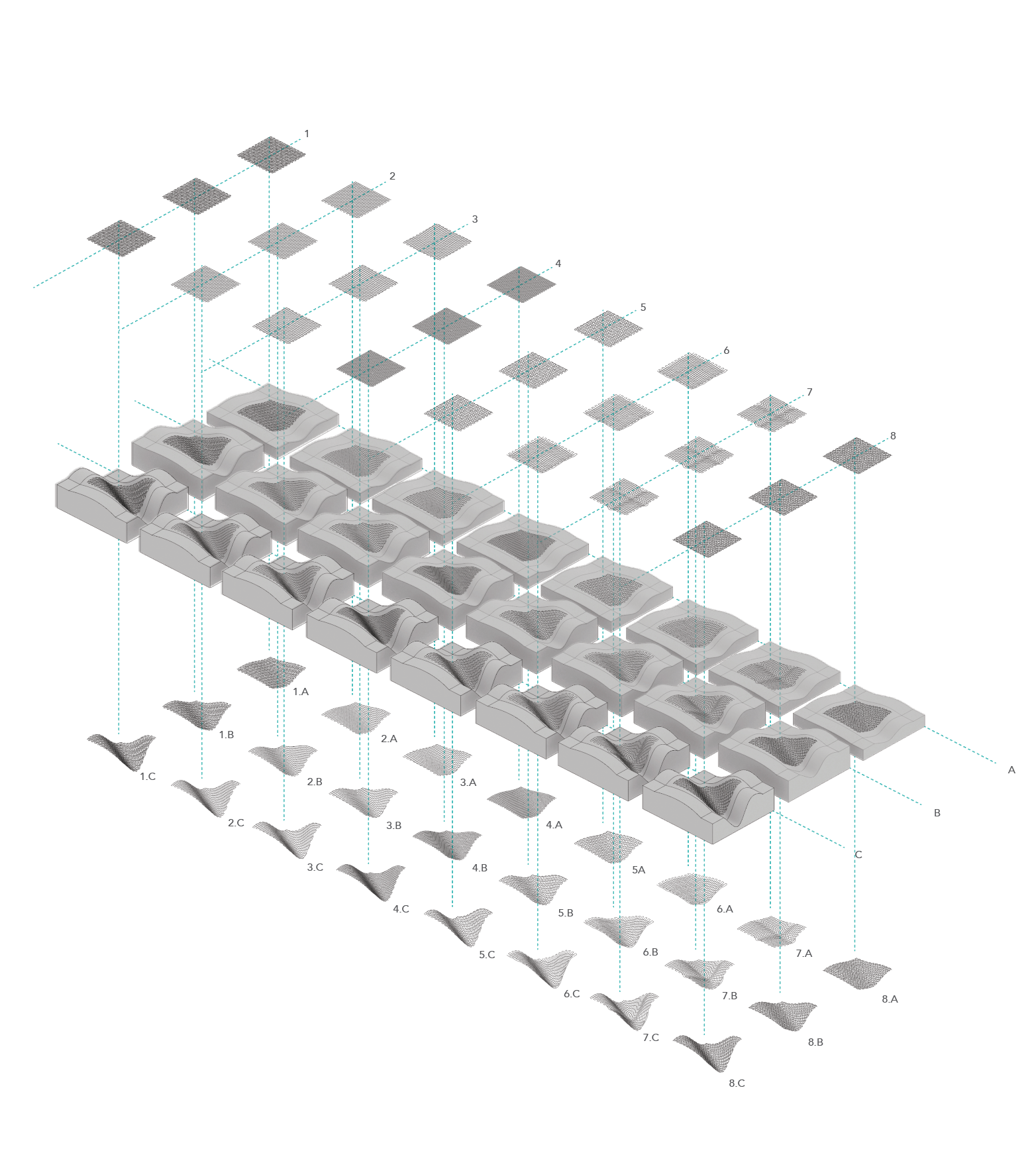
Each tile g-code is printed three times and then slumped over each of the three molds (A, B, C) resulting in variation of opening density through variation in the surface curvature. Layers were printed in pairs of 2, 4, or 6 creating a weave where the structure of the tile is strengthened through the overlap of the clay between layers.
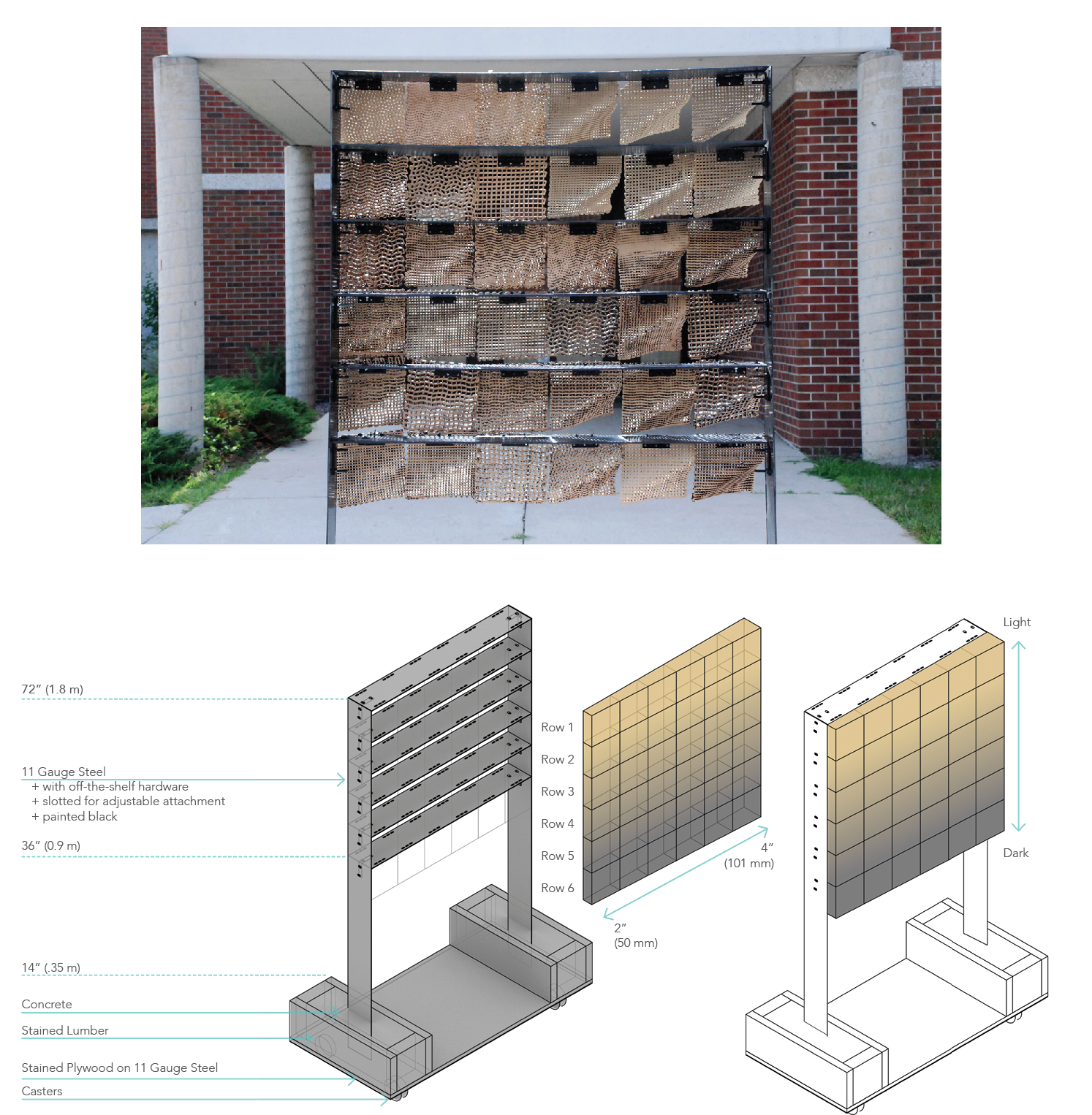
Image, Hardware was attached to the fired tiles using apoxie clay. From the non-glazed (interior) a variety of light conditions and views are created.
Diagram, A full-scale substructure was constructed using Plasma CNC cut steel and off-the-shelf hardware to allow for testing tile assemblies and the development of attachment details. The tiles were hung from lightest to darkest glazing and from smallest curvature to greatest curvature.
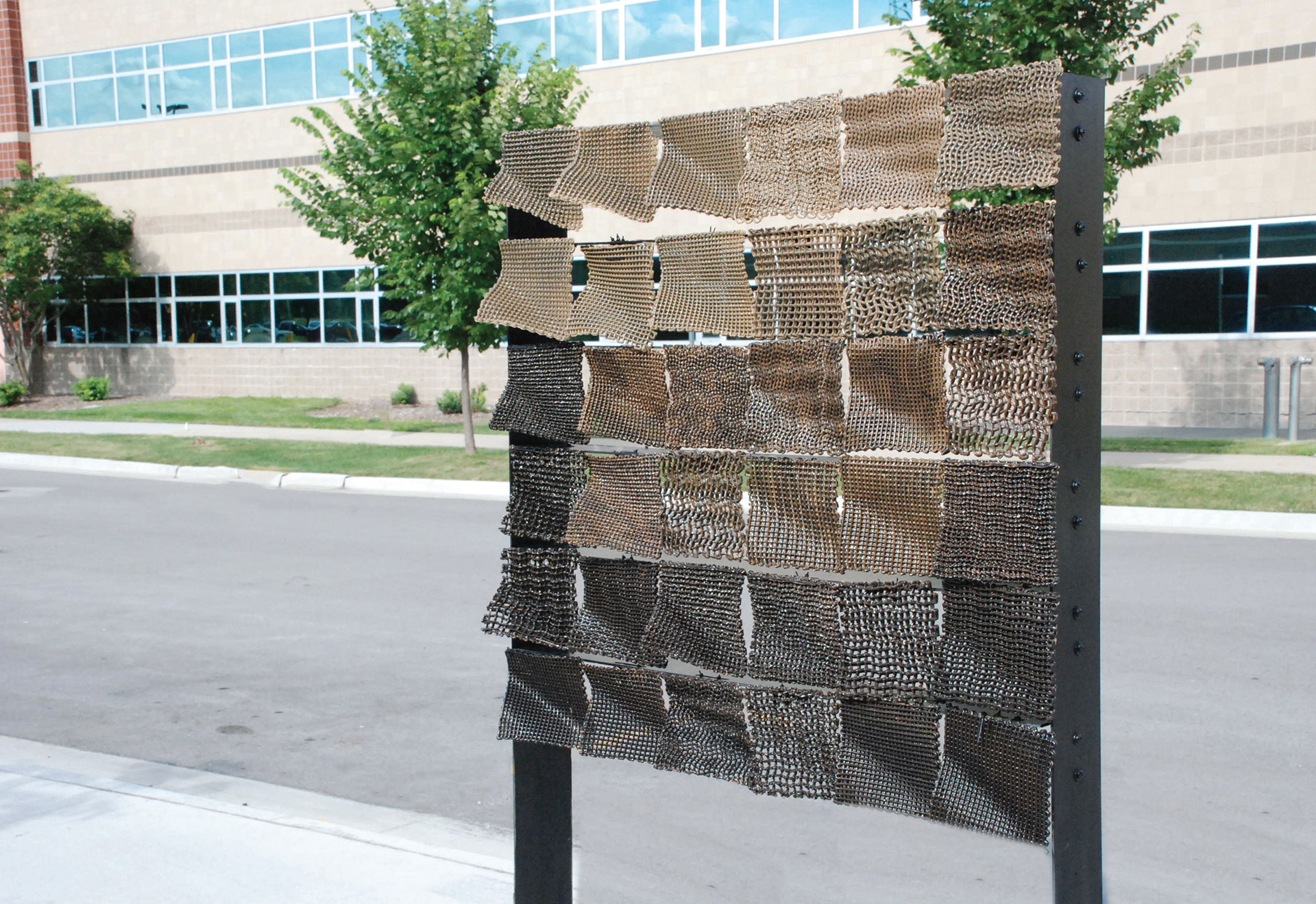
WAFT Mockup
Prep the acrylic base by dampening it with a sponge. Then place a piece of plastic wrap on the acrylic and smooth with a soft pottery rib.
Printing the tile with a Potterbot 7 from Deltabots
Lift up the plastic wrap and slump the tile onto a CNC'd foam mold.
MASON STAINS + PORCELIAN
During the spring semester of 2019, I worked with Kelly Devitt-Steenhagen to develop a workflow for loading porcelain gradients using Mason stains. Students in the Introduction to Digital Fabrication course (for BArch and MArch students at Iowa State University) used pre-loaded porcelain gradients tubes to print custom tiles for the Grasshopper definition that I wrote for Waft. As well as a few new definitions that I helped the student to write. Below are the results of the work from this assignment.
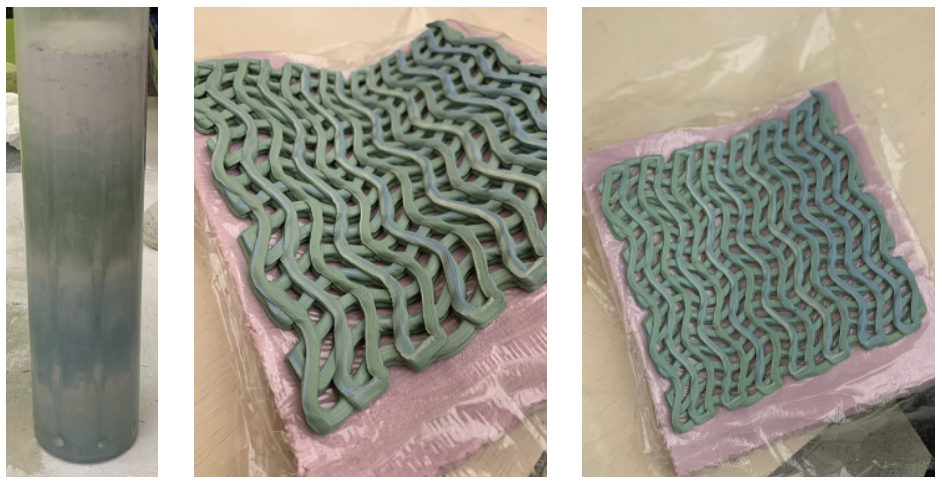
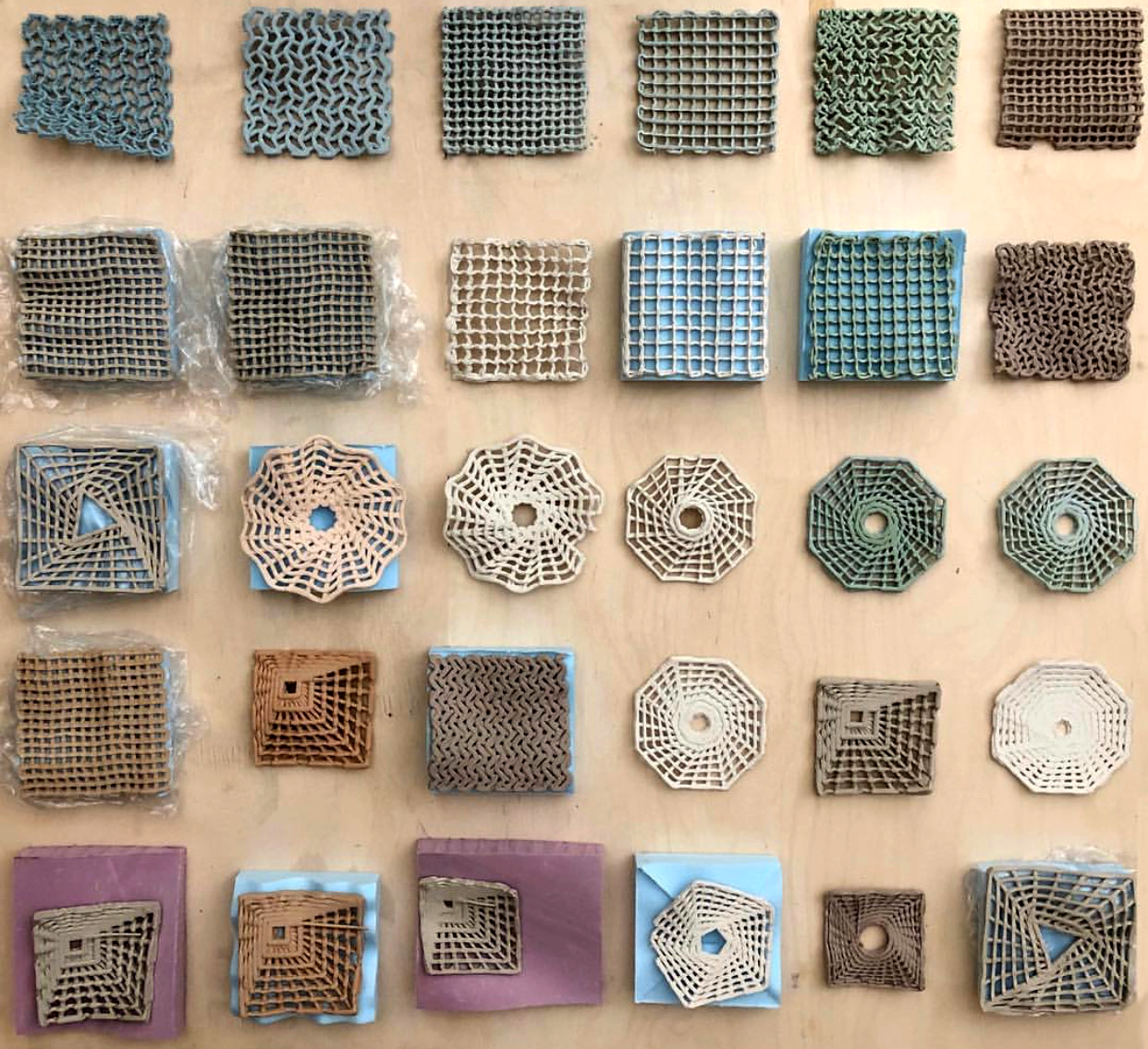