Augmenting Concrete Columns with Water Soluble 3D Printed Formwork
Collaboration with Shelby Doyle
OVERVIEW
Melting is a continuation of prior research conducted in the paper “Dissolvable 3D Printed Formwork: Exploring Additive Manufacturing for Reinforced Concrete” (ACADIA, 2019). The paper proposes simultaneously printing polyvinyl alcohol (PVA) formwork and steel PLA tensile reinforcement to produce water soluble concrete formwork with integrated reinforcement. One conclusion of the paper was that “the complete elimination of formwork may continue to be more preferable than the introduction of biodegradable or water-soluble formworks. The most promising application for these methods might be the augmentation of traditional formwork.” The prototypes that follow use the methods developed in “Dissolvable 3D Printed Formwork” to augment typical concrete construction methods with moments of unique geometry that would be difficult to fabricate using other concrete formwork methods.
FORM A
The top and base design of form A was created by bounding the 3D printed PVA formwork. The boundary was then used to find the curves that touched the top and bottom faces. These curves were polar arrayed and merged into an outer and center curve to create the extruded profile. This method was an attempt to create a smooth transition between the two formwork methods. These profiles were CNC routed from polystyrene insulation foam. Additional custom caps at the top and bottom were CNC routed formwork to hold the 1/2” rebar vertically in position and to connect the two formwork methods. The top layer of CNC routed formwork had additional apertures to allow the Hydraulic Expansion Cement (HEC) to be poured (Figure 5). Although this method allowed for greater formal cohesion and customization it took nearly four hours to CNC route for the single prototype. This formwork was destroyed upon removal and could not be reused limiting it as a replicable strategy. This column used two-thirds of a board of polystyrene insulation foam costing twenty dollars
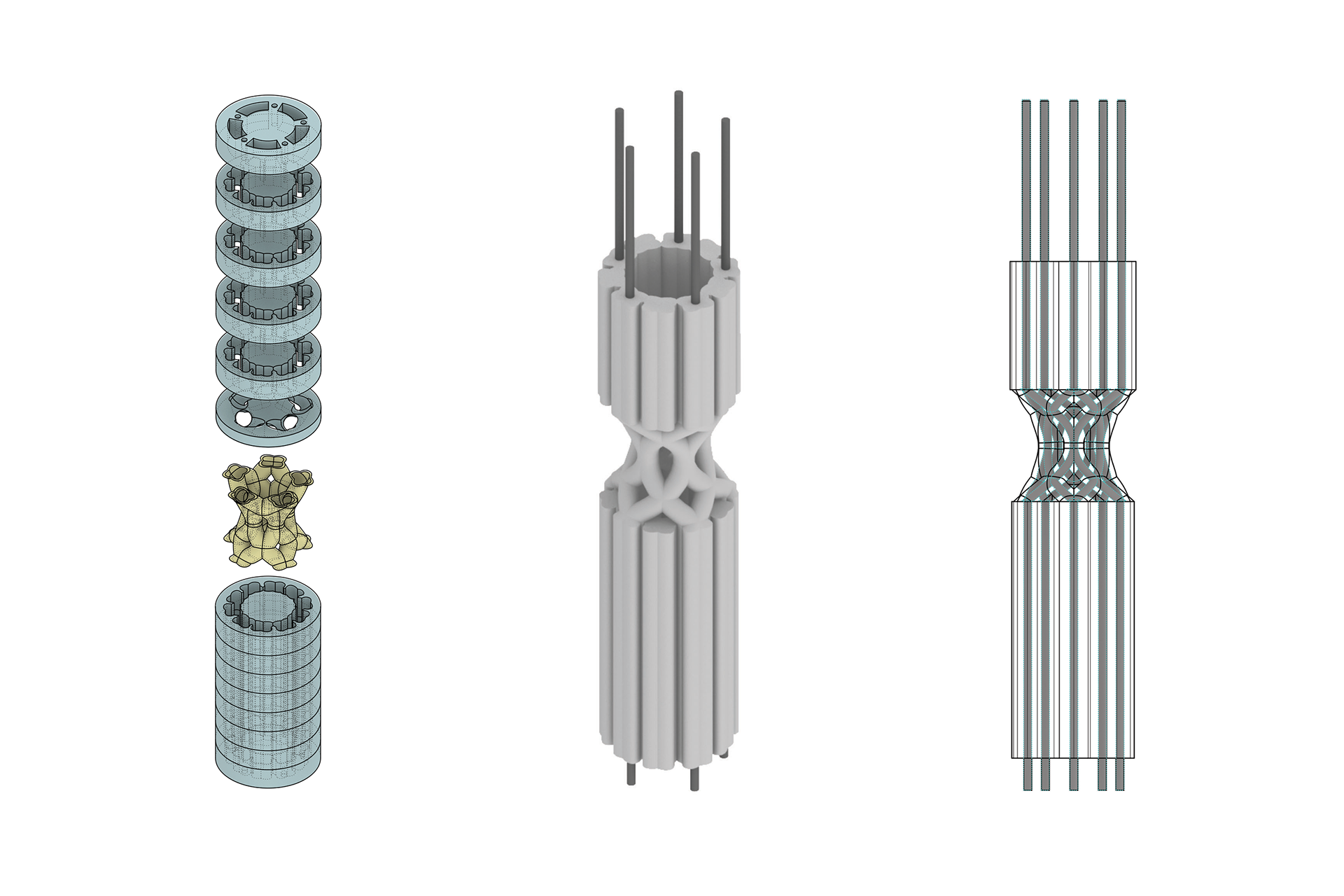
Left to right, diagram of Form A column formwork, rendering of column, and elevation denoting the path of the reinforcement
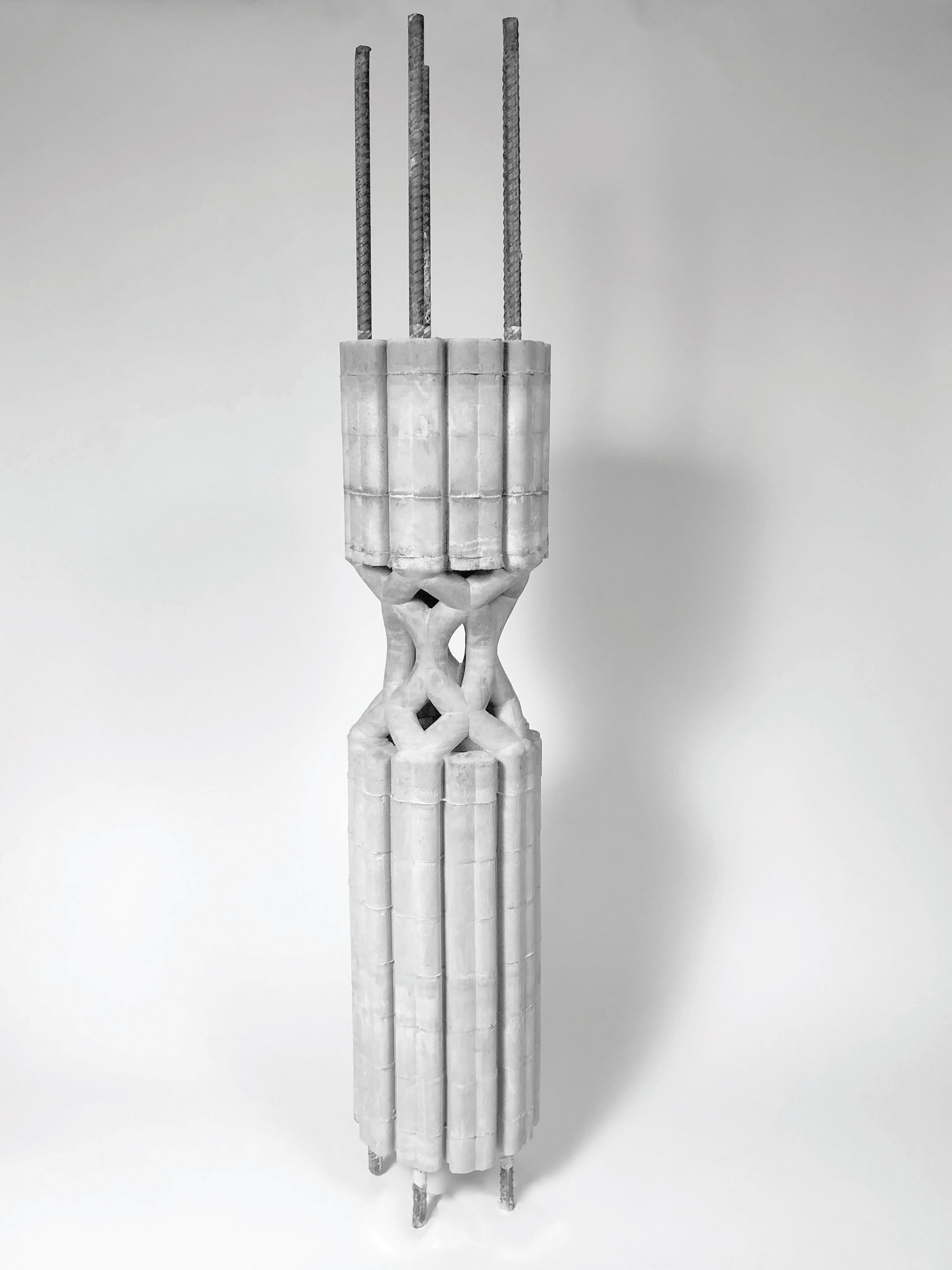
Resulting HEC cast column.
FORM B
These iterations used an eight-inch diameter standard sonotube augmented with PVA formwork. In addition to the sonotubes, four custom CNC routed polystyrene insulation foam caps were created to hold the center off-the-shelf PVC pipes (used to create a hollow cast), 1/2” rebar, and the 3D printed formwork. The CNC’d milled caps allowed for the addition of custom edge qualities such as a chamfer or fillet to create continuity between the 3D printed formworks and the sonotube formworks (Figure 6). Two prototypes were created using this method and a single sonotube costing nine dollars, allowing for a cheaper and faster method than only using water-soluble formwork. Form B-1 had filleted edges (Figure 9) and Form B-2 had chamfered edges (Figure 10) resulting in different resolution of the connection between formwork types. These caps were not damaged upon removal allowing for future reuse. Form B-1 was cast using Quikrete Fast-Setting Concrete with the aggregate sifted out of the mix. This mixture resulted in a less polished surface finish than Form B-2 which was cast using two-parts fine sand one-part cement and one-part water.
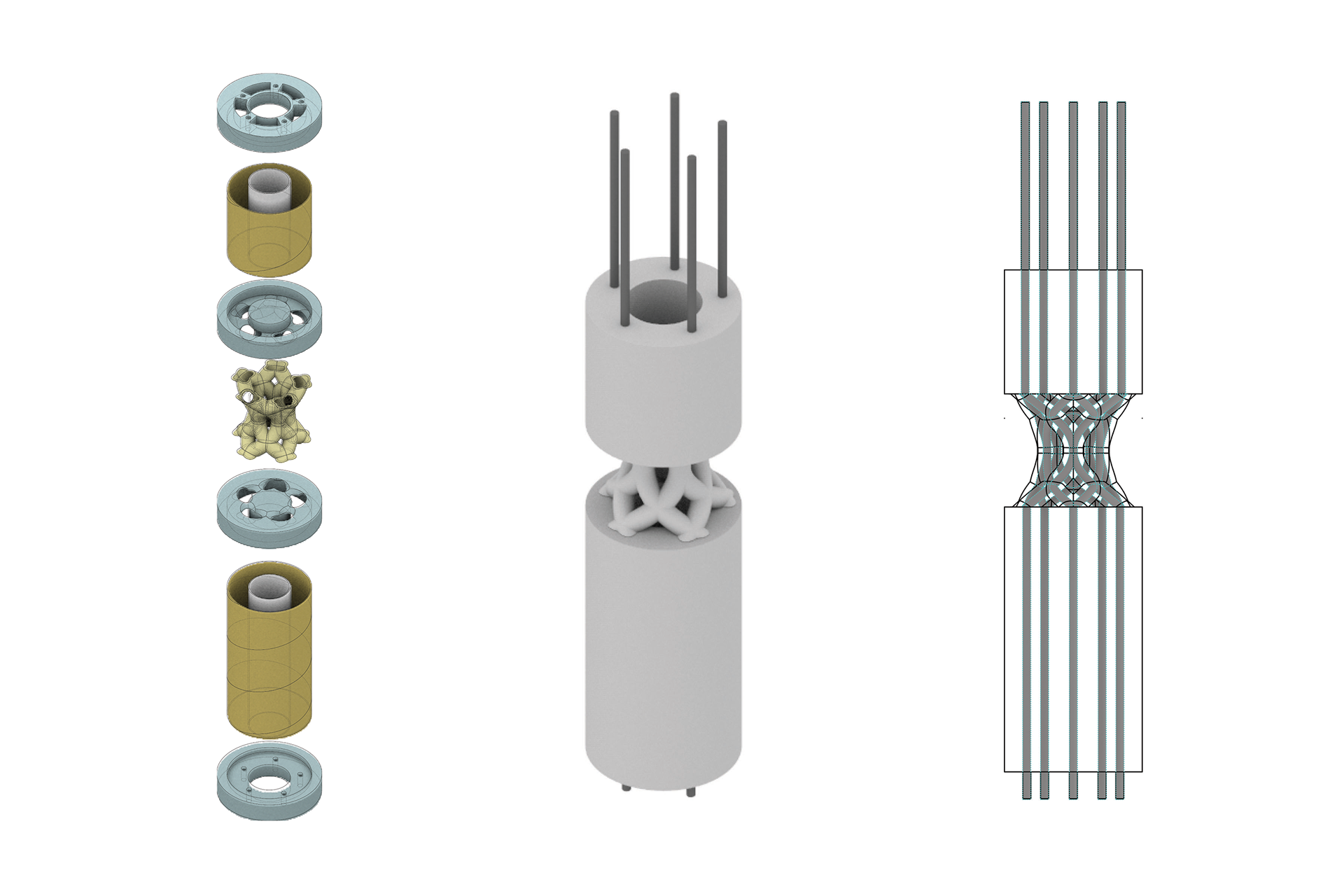
Left to right, diagram of Form B-1+2 column formwork, rendering of column, and elevation denoting the path of the reinforcement.
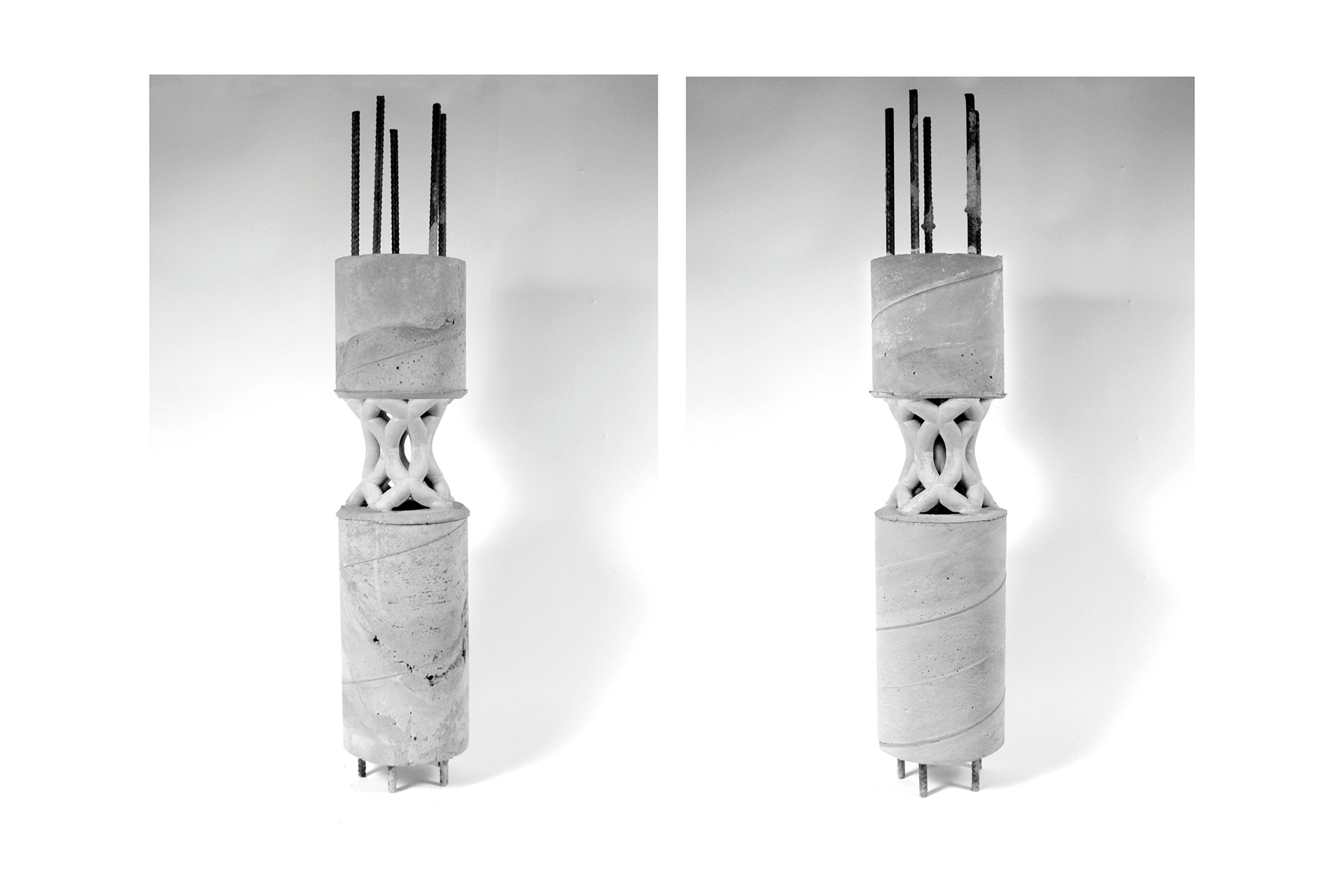
Left: Form B-1 column cast in Quikrete Fast-Setting Concrete with the aggregate sifted out.
Right: Form B-2 column cast using two-parts fine sand one-part cement and one-part water.