Exploring Additive Manufacturing for Reinforced Concrete
Collaboration with Shelby Doyle
ABSTRACT
This research explores the potentials, limitations, and advantages of 3D printing water-soluble formwork for reinforced concrete applications. Using polyvinyl alcohol (PVA) forms and PLA steel tensile reinforcement this project explores the constraints and opportunities for architects to design and construct reinforced concrete using water soluble 3D printed formwork with embedded reinforcement. Research began with testing small PVA prints for consistency, heat of water-temperature for dissolving, and wall thickness of the printed formwork. Then, dual-extrusion desktop additive manufacturing was used as a method for creating a larger form to test the viability of translating this research into architectural scale applications. This paper describes the background research, materials, methods, fabrication process, and conclusions of this work in progress.
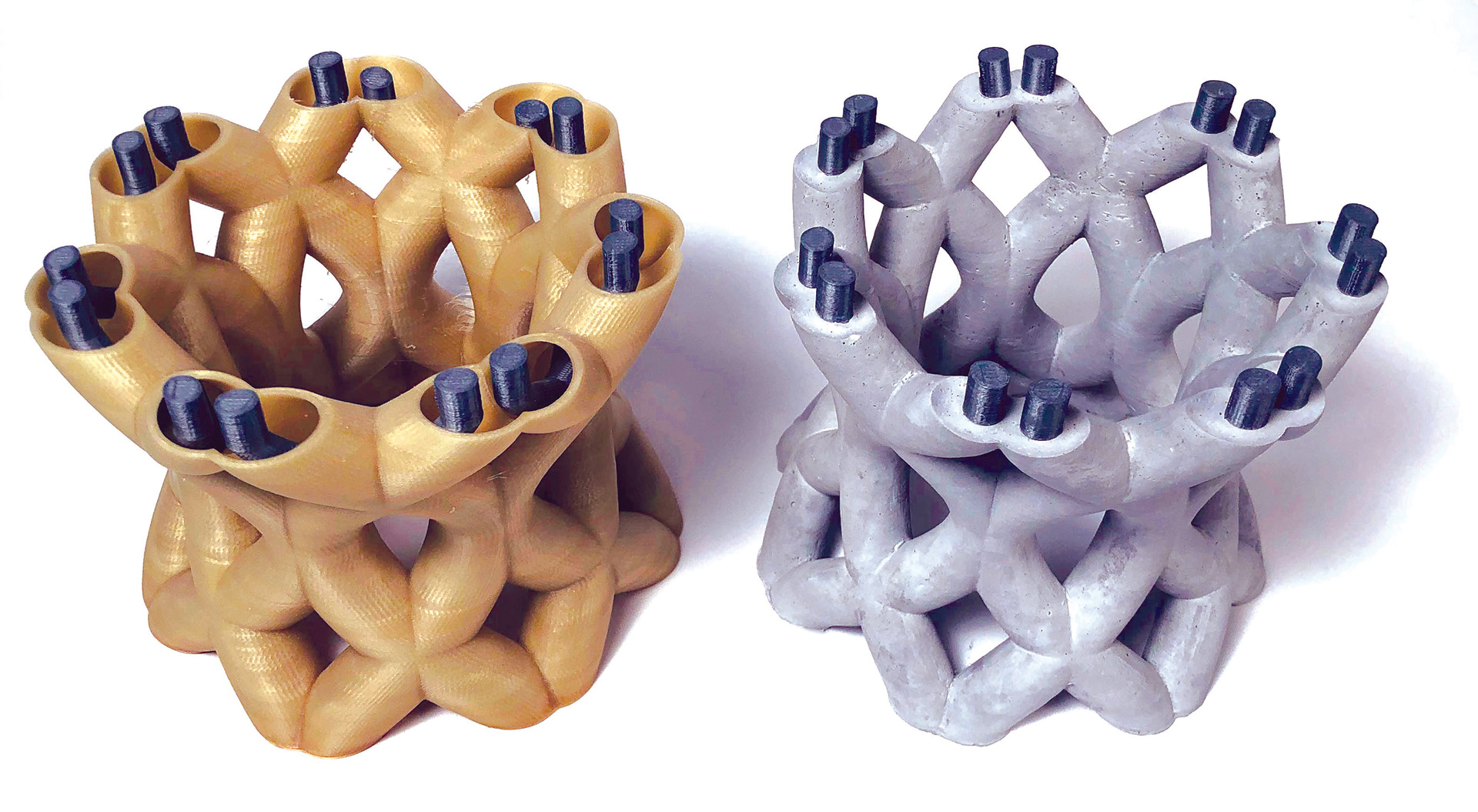
On the left, PVA form with embedded PLA printed reinforcement. On the right, resulting HEC (Rockite) cast form with embedded PLA reinforcement after the PVA was dissolved with water.
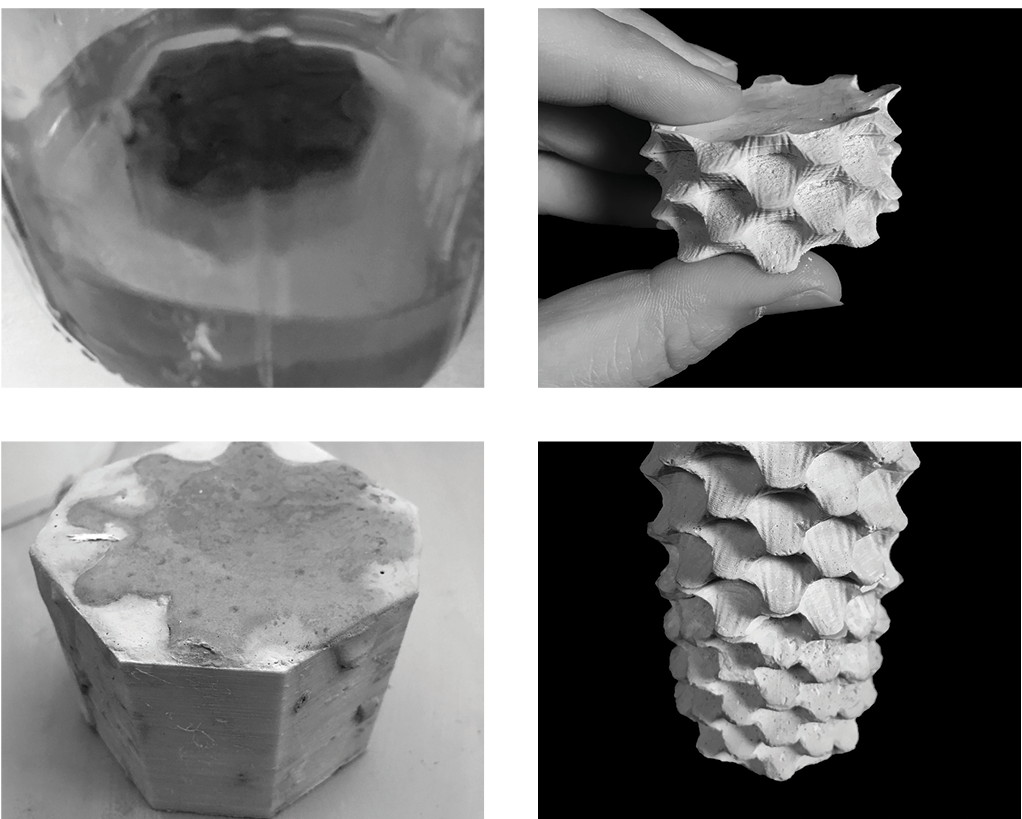
Early iterations of printing soluble formwork to the left two images used HIPS filament and dissolved with D-Limonene and the right two images used water soluble HIGH-T-LAY.
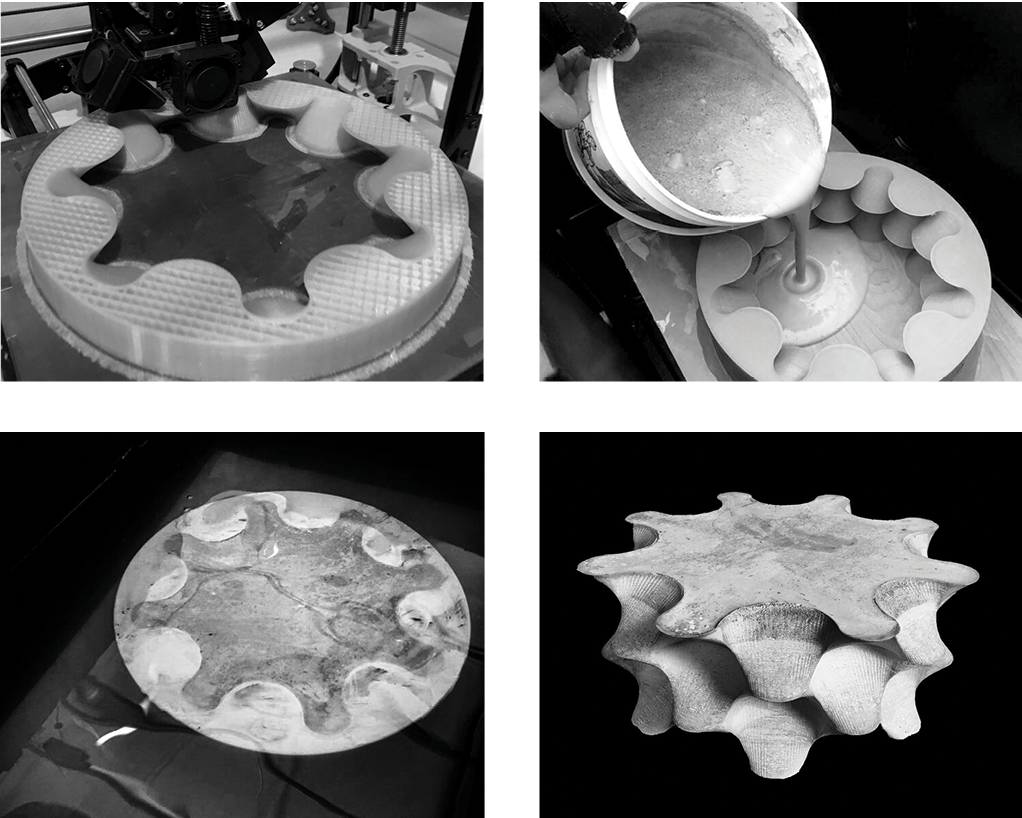
Once the use of PVA was established a larger scale (9” / 225 mm diameter) mold was printed and poured with HEC (Rockite) to determine whether the PVA might continue to work at a larger scale. The mold was 4” (101 mm) tall and took 58 hours to print at standard resolution or 0.25 mm layer height.
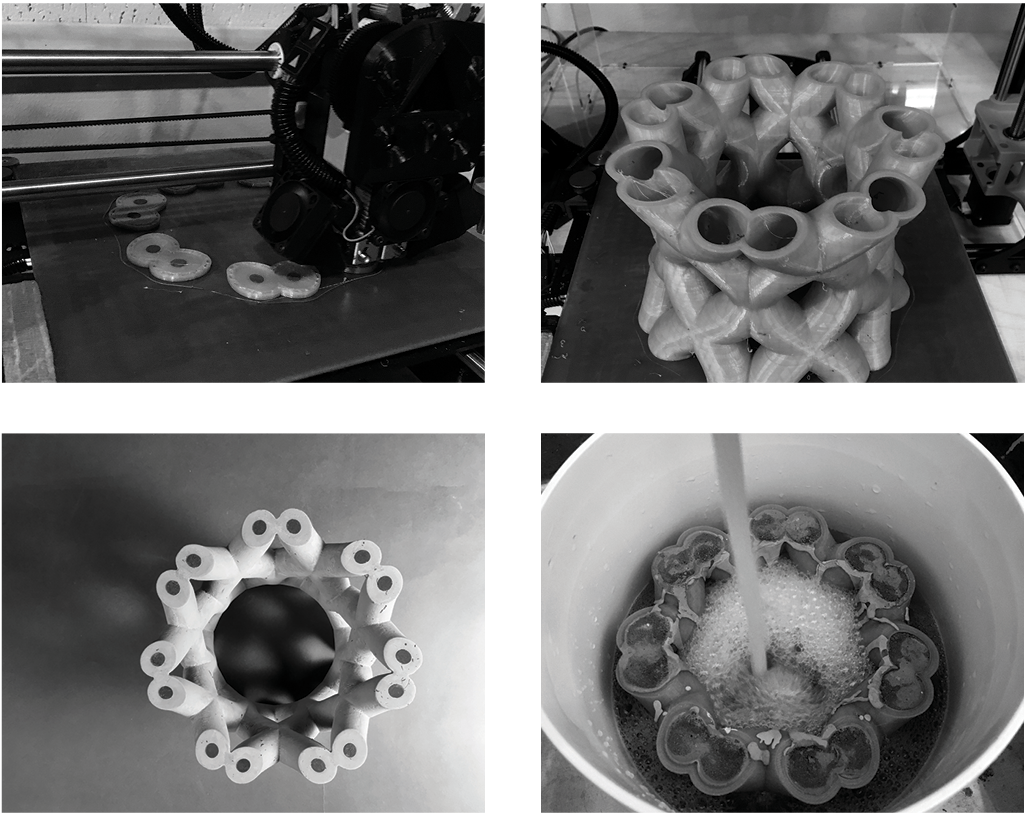
The next step was to attempt to print both PVA and PLA/Steel Filament simultaneously to determine whether steel reinforcement might be placed within a geometrically unique formwork. Early tests required the calibration of temperature settings for the PLA/Steel filament as it was more brittle than the PVA and more likely to break or fail during prints.
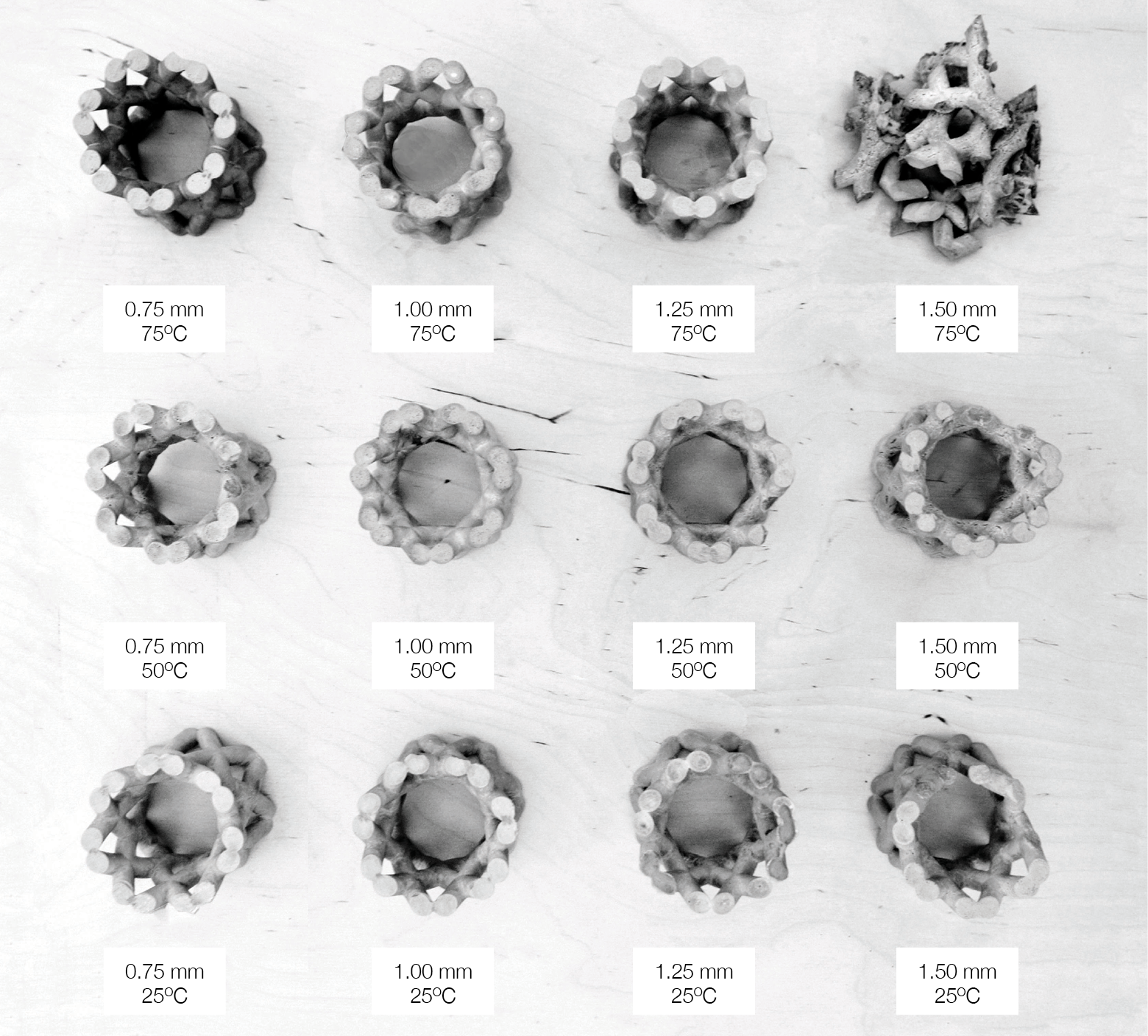
Initial tests were conducted using three temperatures determine the most suitable for dissolving PVA. The three temperatures selected were 25, 50 and 75° Celsius. The samples dissolved in the 75° Celsius water dissolved more rapidly as well as requiring less frequent water changes. After twenty-four hours all samples required further cleaning with a brush and water. The amount of cleaning was inversely proportional to the water temperature. Different shell thicknesses were also evaluated: 0.75, 1.00, 1.25, 1.5 millimeters. The thinnest walls dissolved most rapidly when placed in the 75° water
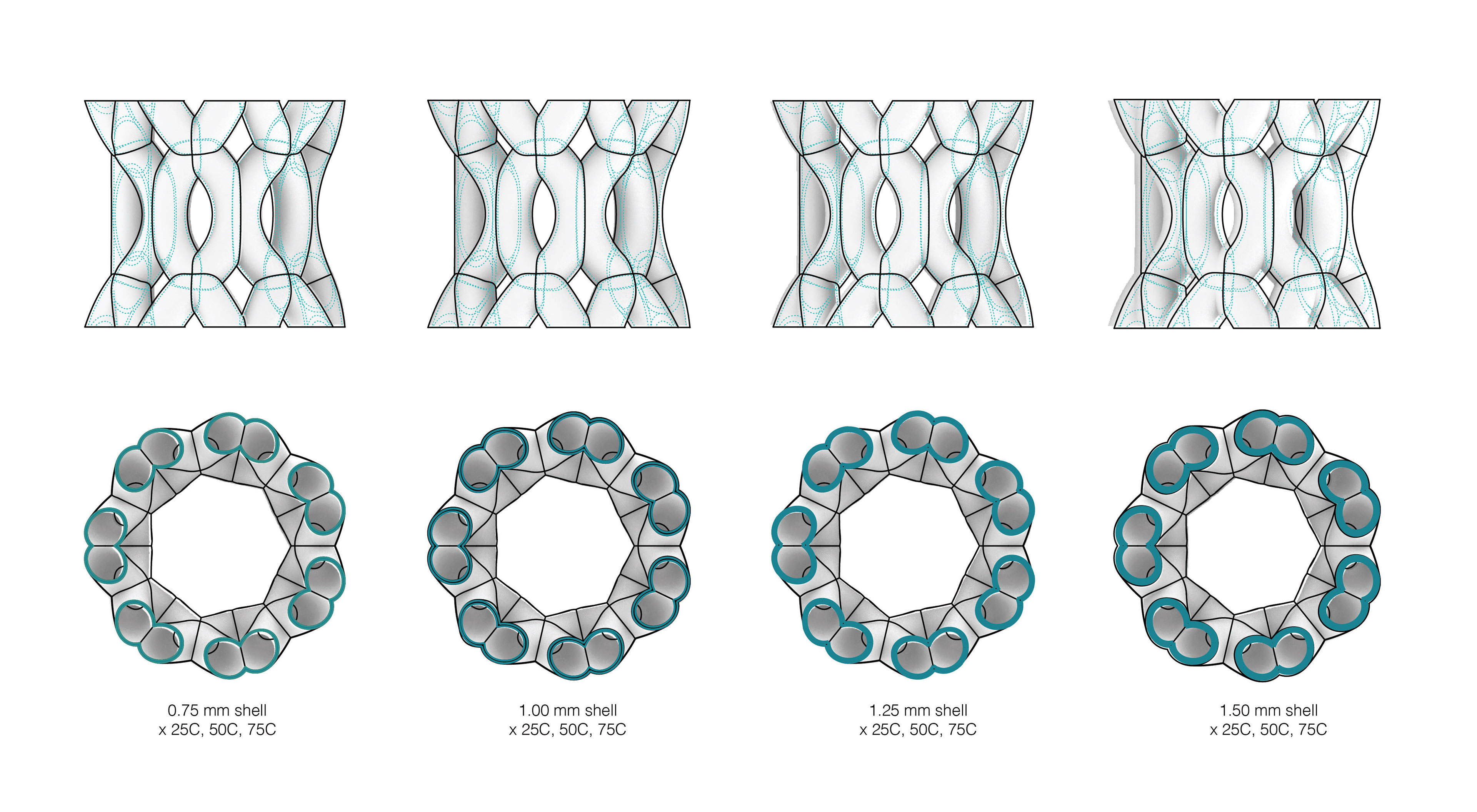
Early iterations testing PVA shell/mold thickness and temperature for dissolving the PVA. From left to right 0.75, 1.00. 1.25, and 1.5 mm shell/mold thickness and from bottom to top 25°, 50°, and 75° Celsius water temperature for dissolving. The thinnest shell and highest temperature performed best.
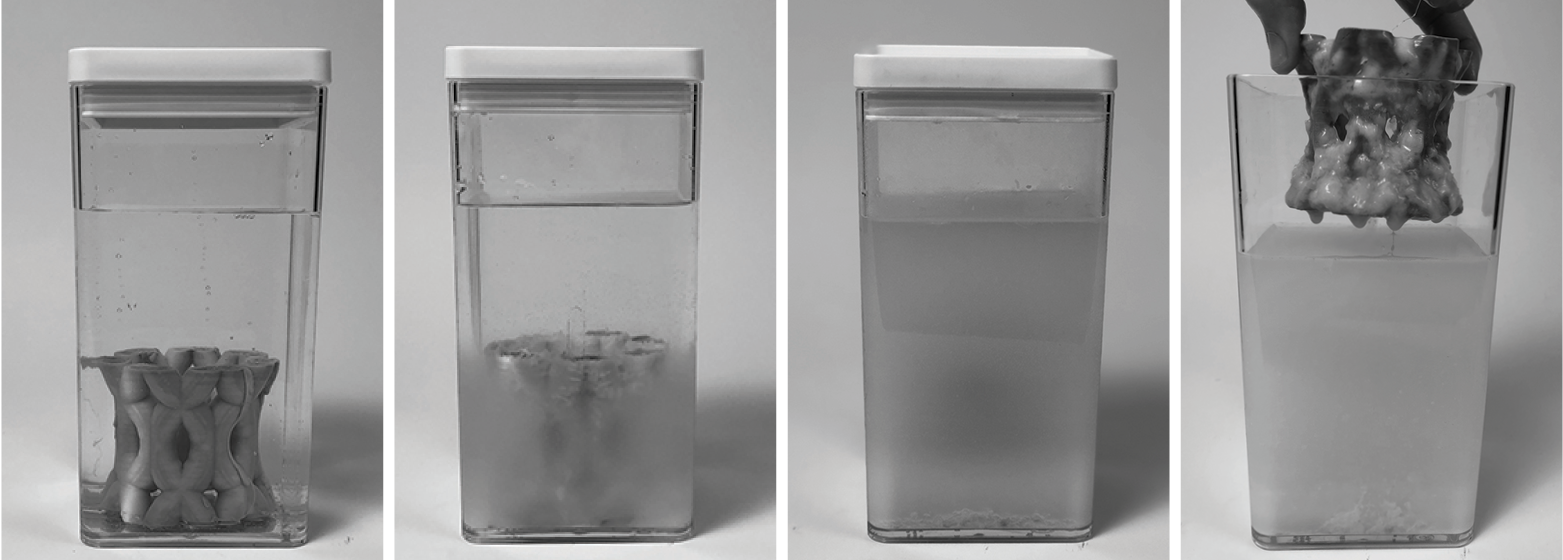
Photos of PVA during the dissolving process of a 1.00 mm shell PVA cast with HEC in 50° Celsius water. From left to right: hour 0, 4, 8, and 12. Dissolving completed after 24 hours.
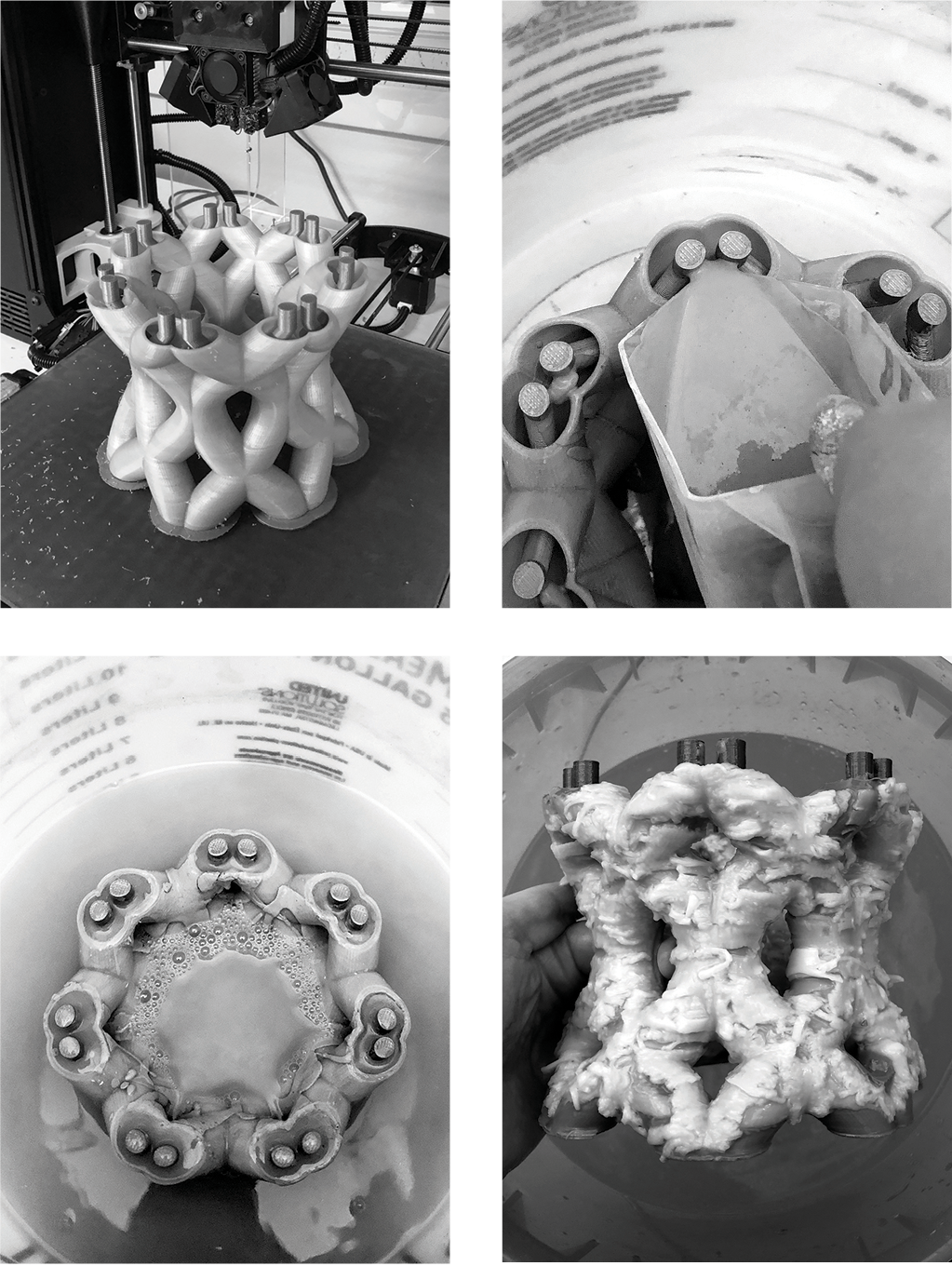
Photos of the final test process. Clockwise from top left: printing, casting, cleaning, and soaking.
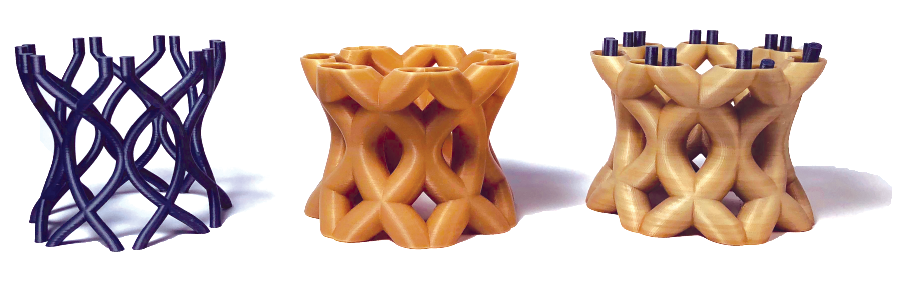
To the left is the embedded reinforcement printed separately for clarity, in the middle the PVA mold printed separately for clarity, and to the right the PVA mold printed with embedded reinforcement.
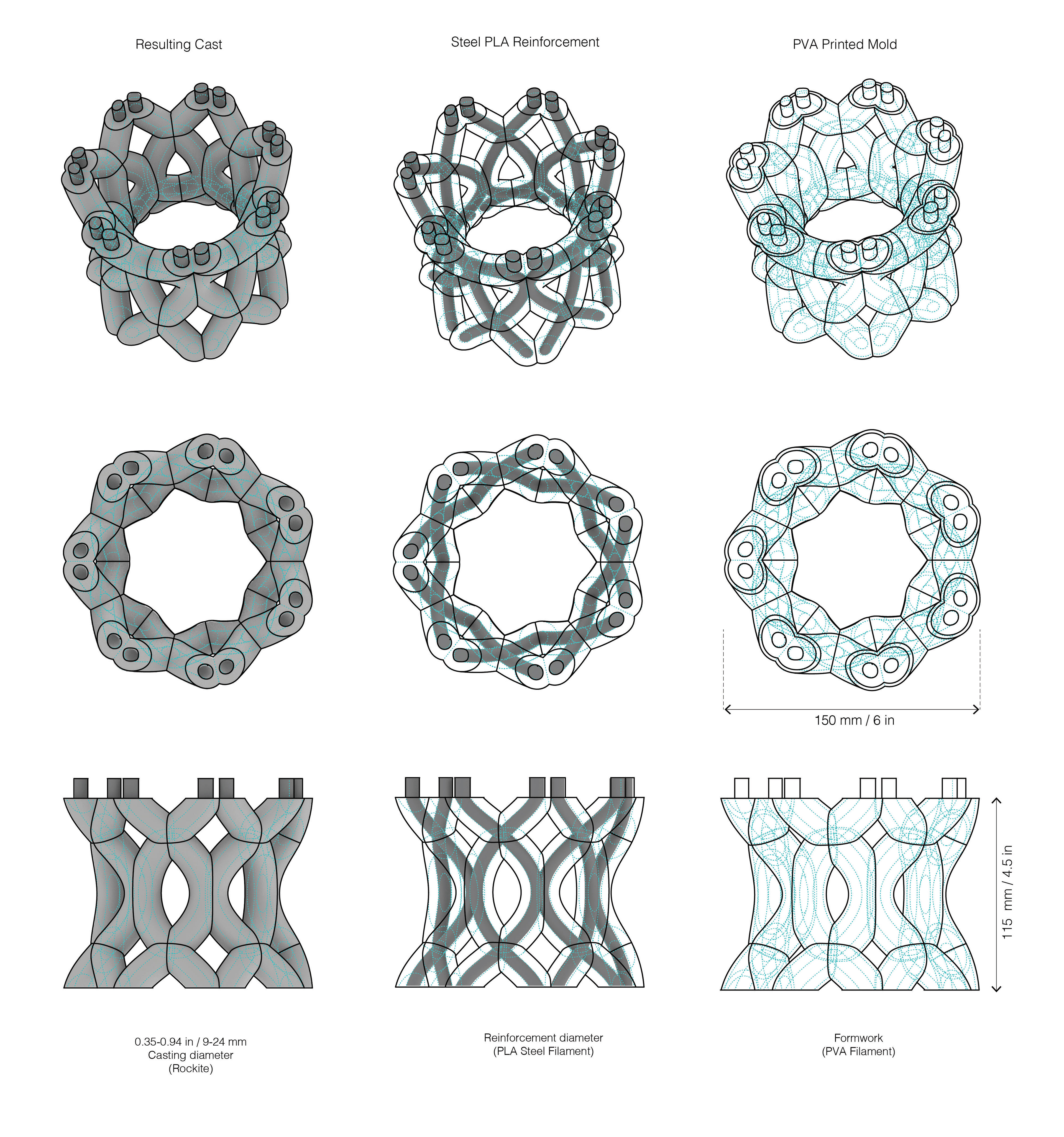
Drawings of the final design.
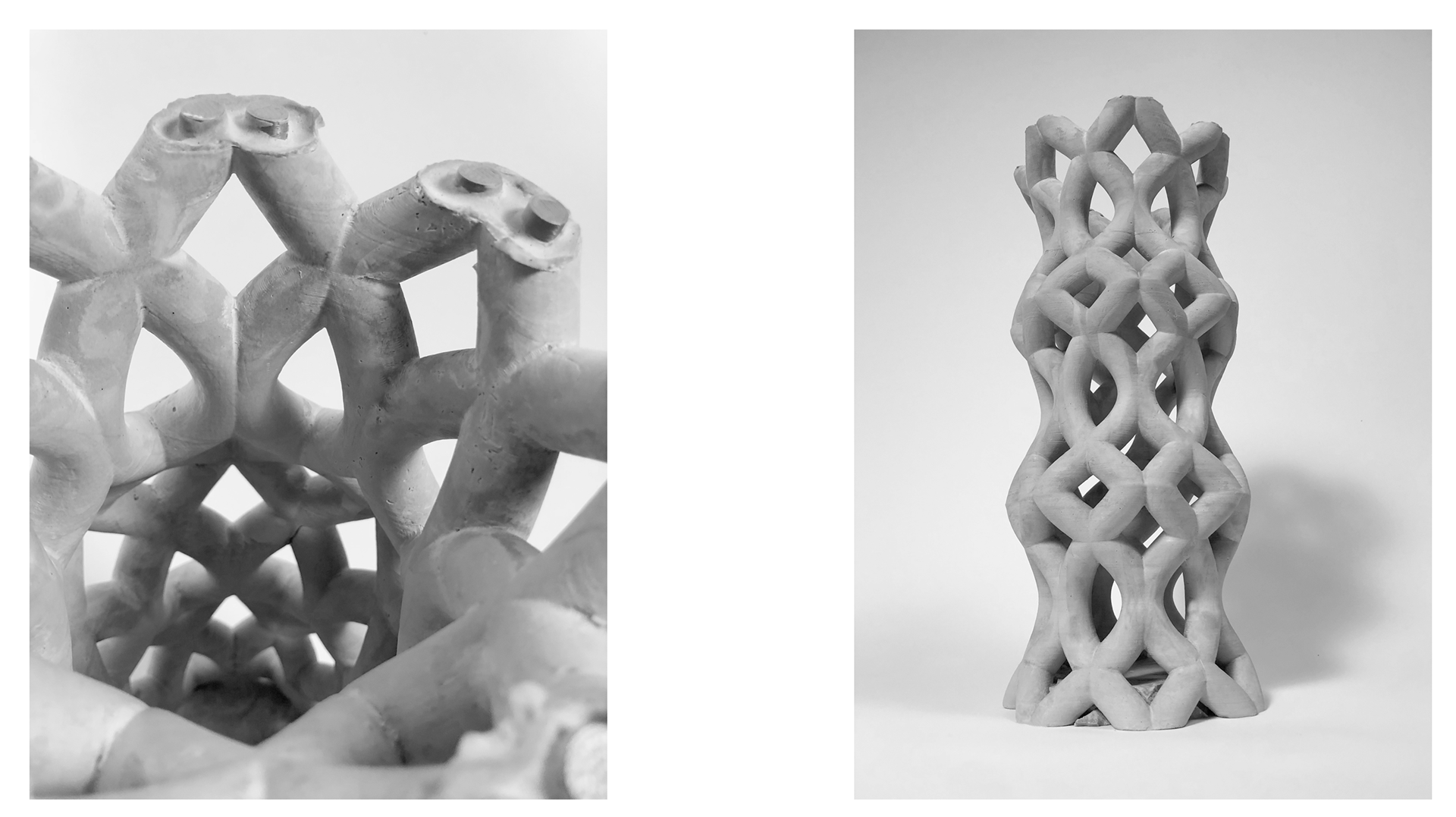