Augmenting Concrete Columns with Water Soluble 3D Printed Formwork
Collaboration with Shelby Doyle
ABSTRACT
This project investigated computational design and fabrication methods for locating standard steel reinforcement within 3D printed water-soluble PVA formwork to create non-standard concrete columns. Each column is eight-inches in diameter and hour feet tall and reinforced with five standard #3 reinforcement bars. Methods from the prior fabrication investigations were adapted for larger-scale construction including the introduction of the tool head with the 1.2 mm nozzle. The Woven column design advances the research presented in Dissolvable 3D Printed Formwork using a new and larger nozzle for desktop scale fabrication. The aforementioned HS+ tool head reduced printing time ant this design explore how geometry can be used to mask the location of the standard reinforcement through the appearance of woven “strands” of concrete. Additionally, the design removes any interior concrete that is not necessary to provide minimum rebar coverage, reducing the material used. Initial research plans included 3D printing continuous molds with a KUKA-1100 industrial robotic arm. Although as a result of the COVID-19 pandemic lab access ceased. Since this was the first time that the robotic arm would be used for 3D printing it was determined that a design the used a single, continuous toolpath would be used so material retraction would not need to be considered. Since the quarantine left desktop fabrication as the only option, a design which required retraction as a result of its apertures was explored. This design exploration resulted in the Aperture column. This Grasshopper definition placed various openings in locations where rebar was not present.
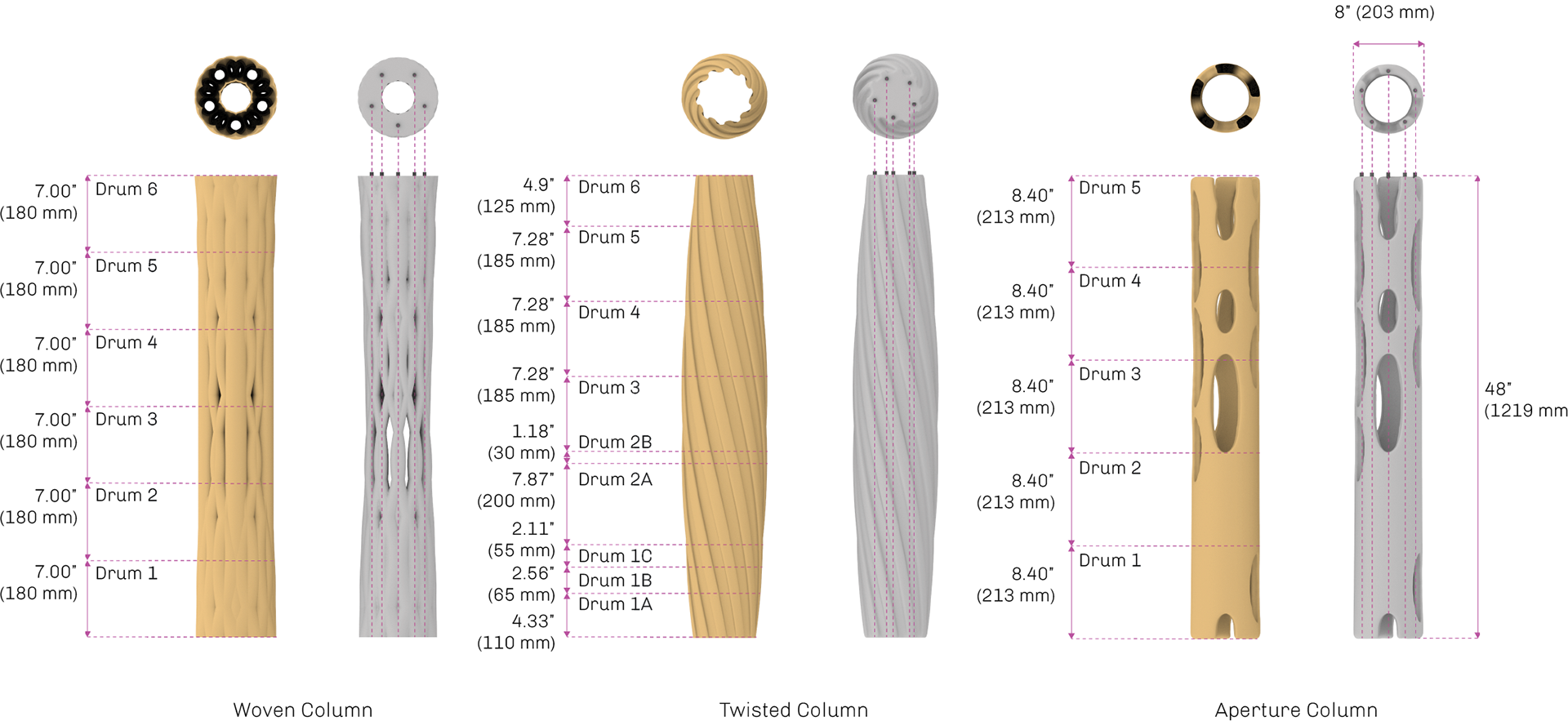
The diagram above indicated how the mold was segmented for desktop fabrication on the LulzBot TAZ 6 FDM printer with the HS+ tool head. Each drum indicates a single print.
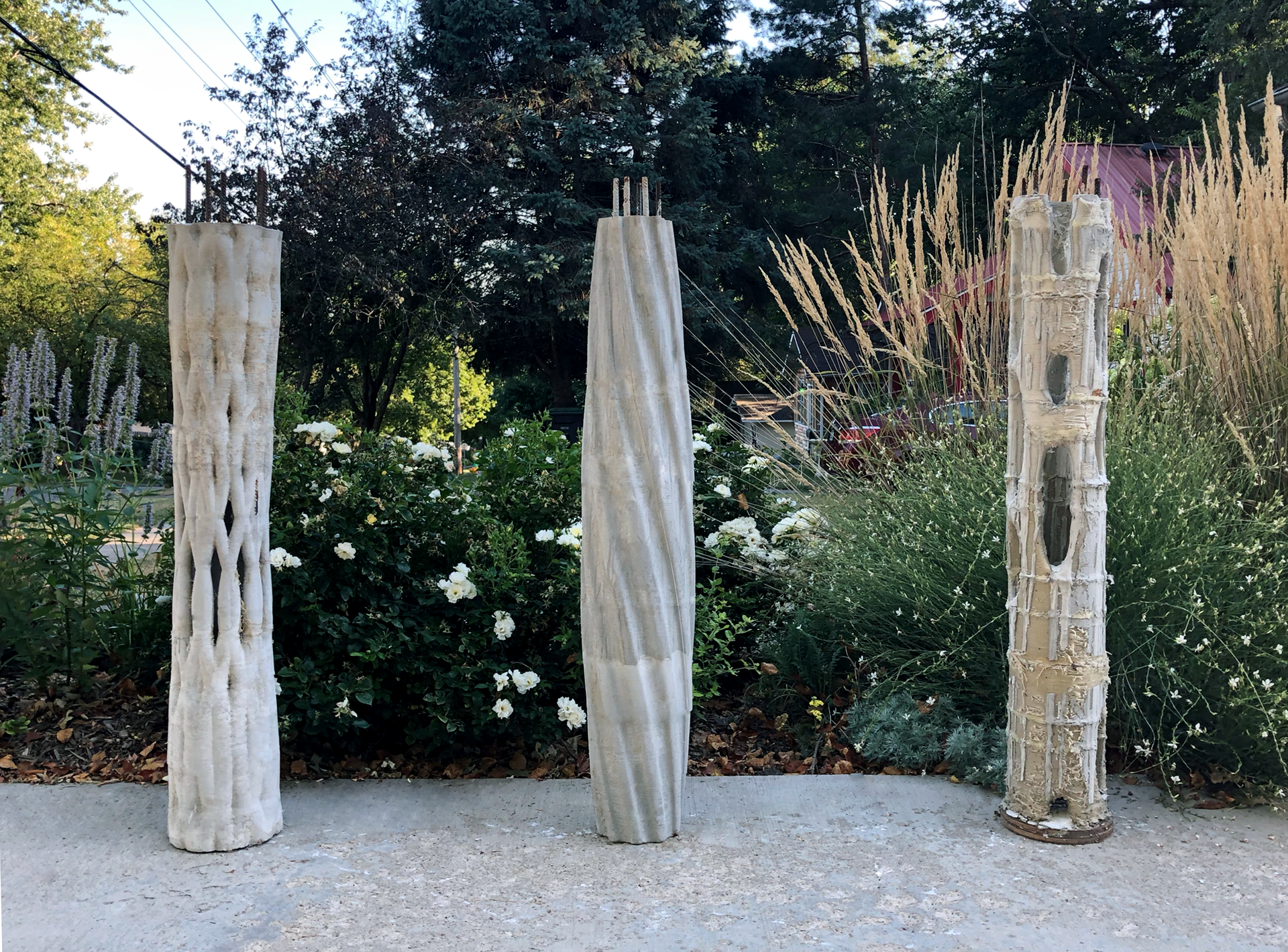
This image above shows the three columns after casting: Woven, Twisted, and Aperture. This photo was taken in June when the Aperture Column was still enclosed in its PVA formwork.
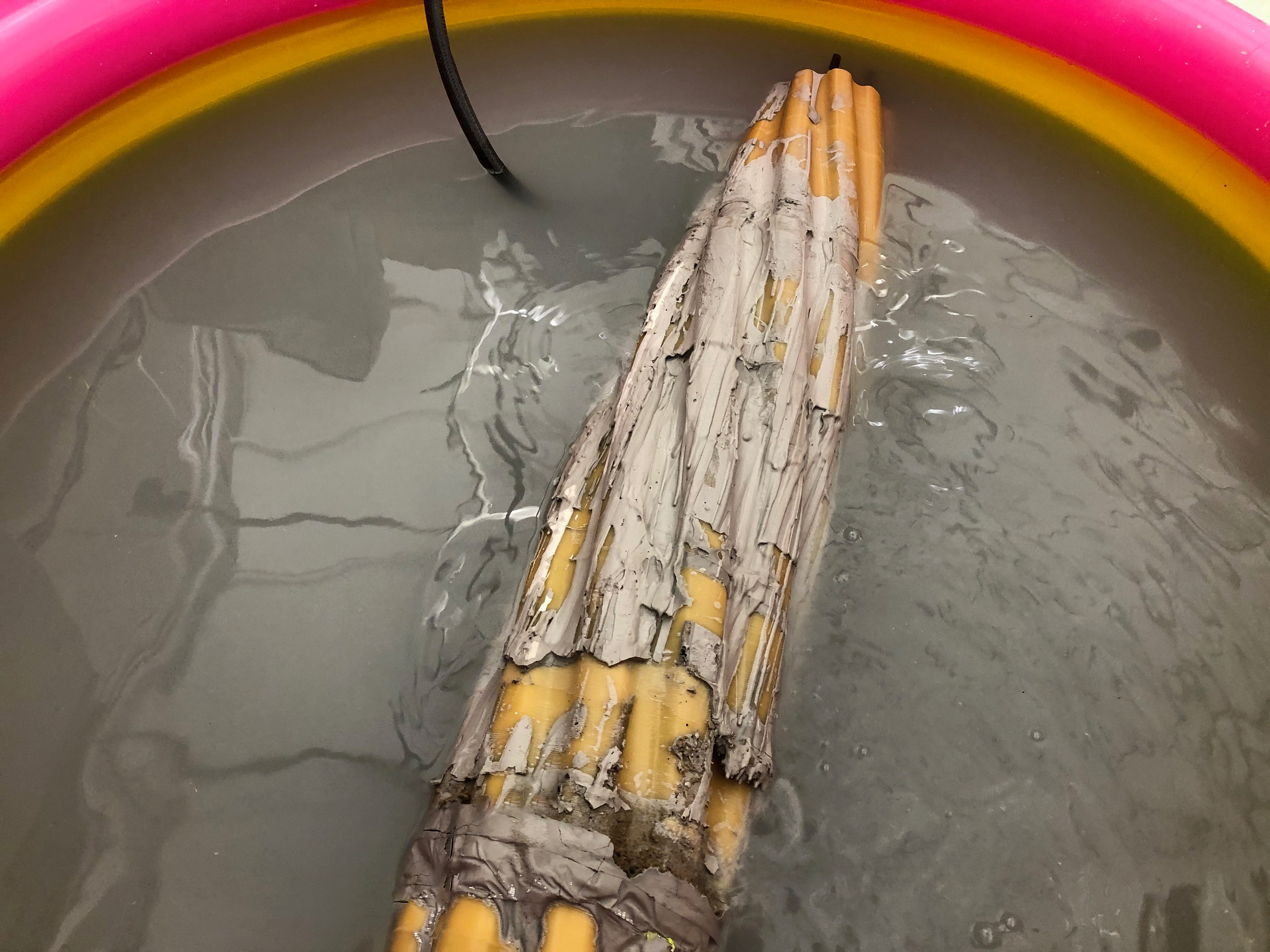
A small, inflatable pool was purchased to dissolve the PVA formwork from the column. This process took a few hours. Both the Woven and Twisted Columns' formwork was dissolved using this process.
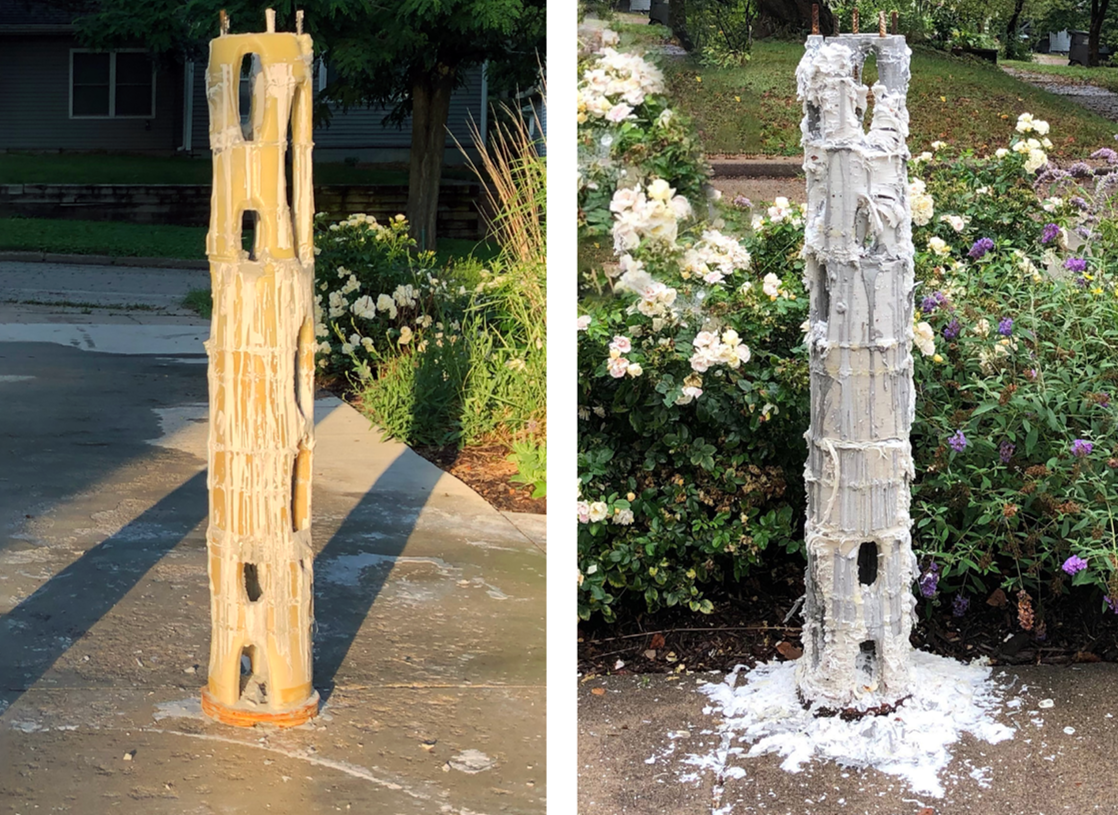
As a result of the remote fabrication, it was possible to leave the Aperture Column outdoors for six months to determine if it was possible to dissolve the formwork solely through exposure to weather. The image at left is the column immediately after casting in June of 2020. The image at right was taken in four months later in October 2020 after four months of exposure.
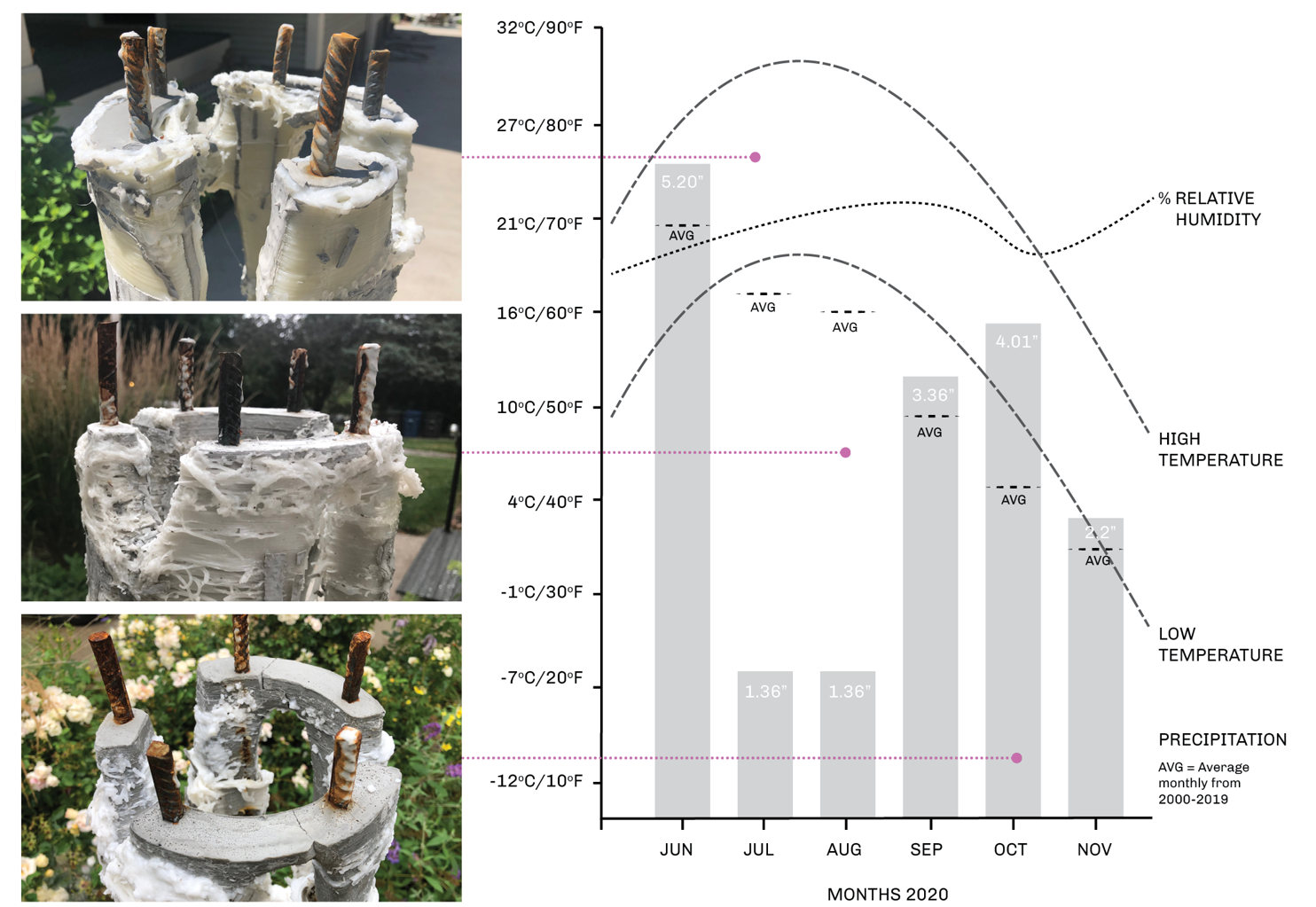
The Aperture Column was exposed to six months of weather conditions. The images at left correlate with the weather conditions from June-December 2020: high and low temperature, relative humidity, and precipitation. A drought in July and August was followed by above average precipitation in September-November.
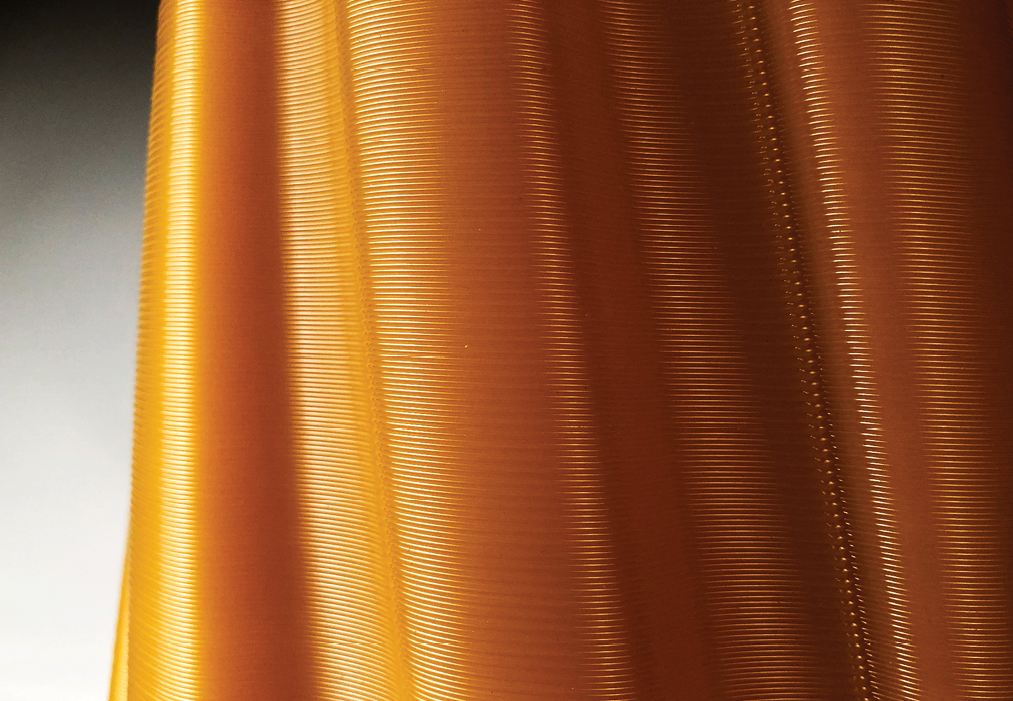
Twisted Column PVA formwork detail before casting.
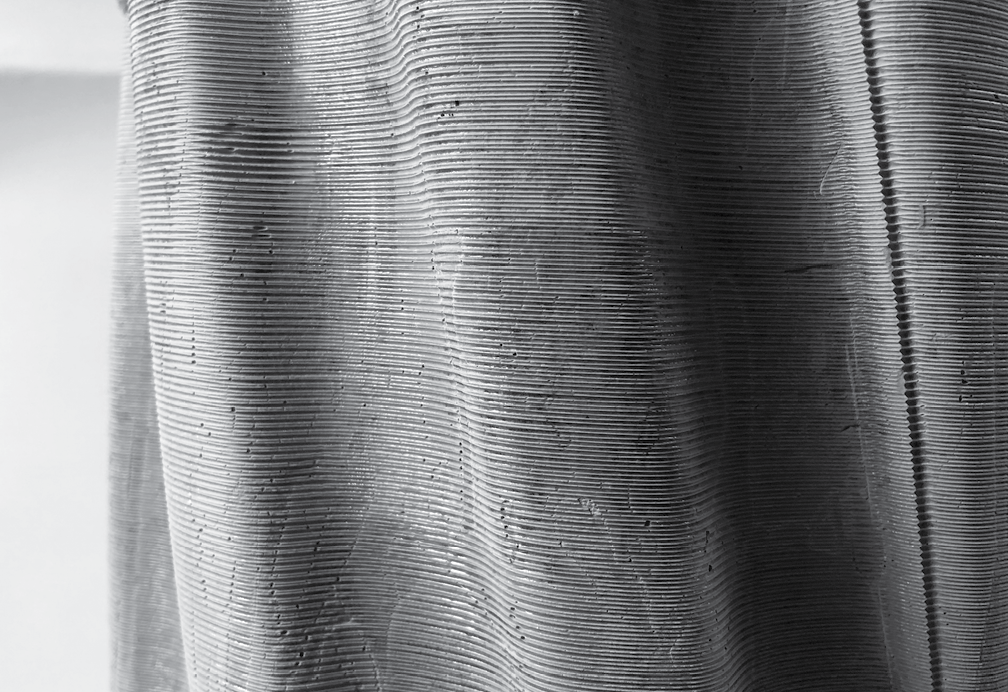
Twisted Column after casting and PVA formwork dissolved.