This research explores the potential of custom 3D printed nozzles for use in ceramic 3D
printing. A single digital model was used throughout the process thereby limiting the test
parameters to nozzle geometry and print speed. Despite beginning each iteration with an
‘idealized’ computational model the subsequent work resulted in unforeseen results and
imprecisions. The nozzles, as low-cost and small-scale interventions, introduce new
possibilities for future design and architectural applications with ceramic 3D printing.
These possibilities include embedding computational analysis for performative
applications, such as the movement of water, with aesthetic outcomes, such as density
and patterning gradients.
printing. A single digital model was used throughout the process thereby limiting the test
parameters to nozzle geometry and print speed. Despite beginning each iteration with an
‘idealized’ computational model the subsequent work resulted in unforeseen results and
imprecisions. The nozzles, as low-cost and small-scale interventions, introduce new
possibilities for future design and architectural applications with ceramic 3D printing.
These possibilities include embedding computational analysis for performative
applications, such as the movement of water, with aesthetic outcomes, such as density
and patterning gradients.
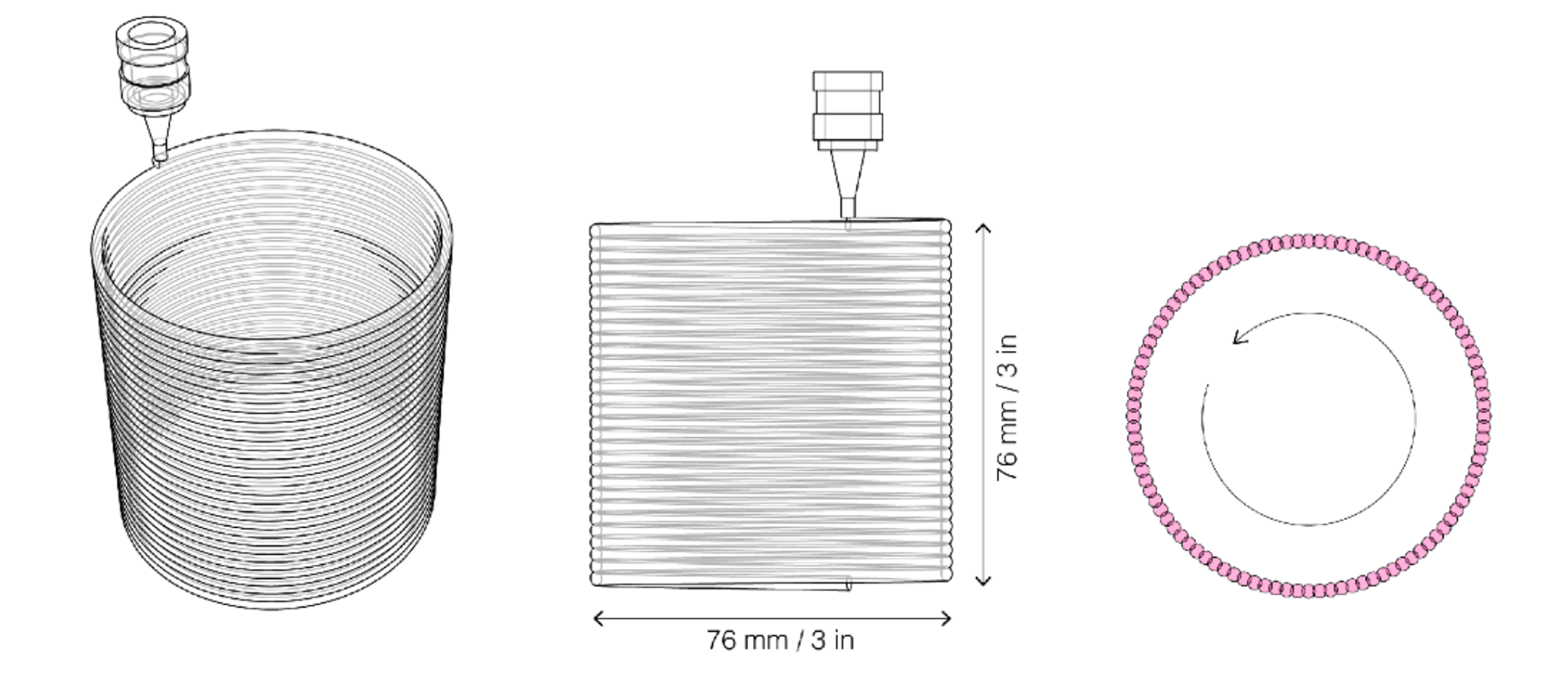
Diagram of the standard 3 mm Potterbot nozzle printing a 76 mm (3”) x 75 mm (3”) cylinder. From left to right: axon, elevation, plan.

Beginning iterations of nozzle designs. The arrayed holes of the “A” group divided the clay into too many strands thereby preventing adhesion between the layers, clogging the nozzle, and compromising the structure of the cylinder. The width of the “B” group spread the clay horizontally creating a wide cylinder wall and very little geometric trace on the vertical face of the cylinder. The asymmetry of the geometry in the “C” group prevented adhesion between the layers as the clay was unevenly applied and compromised the structure of the cylinder. The horizontal plane of the “D” group flattened the patterning due to the flush surface surrounding the aperture. The sharp corners of the “E” group proved most successful in producing patterns and shadow lines in the clay due to the combination of the circular motion of the print bed and the twisting of the clay as it was deposited by the nozzle. As the cylinder prints, the outward facing corner changes as it rotates producing a visible edge.
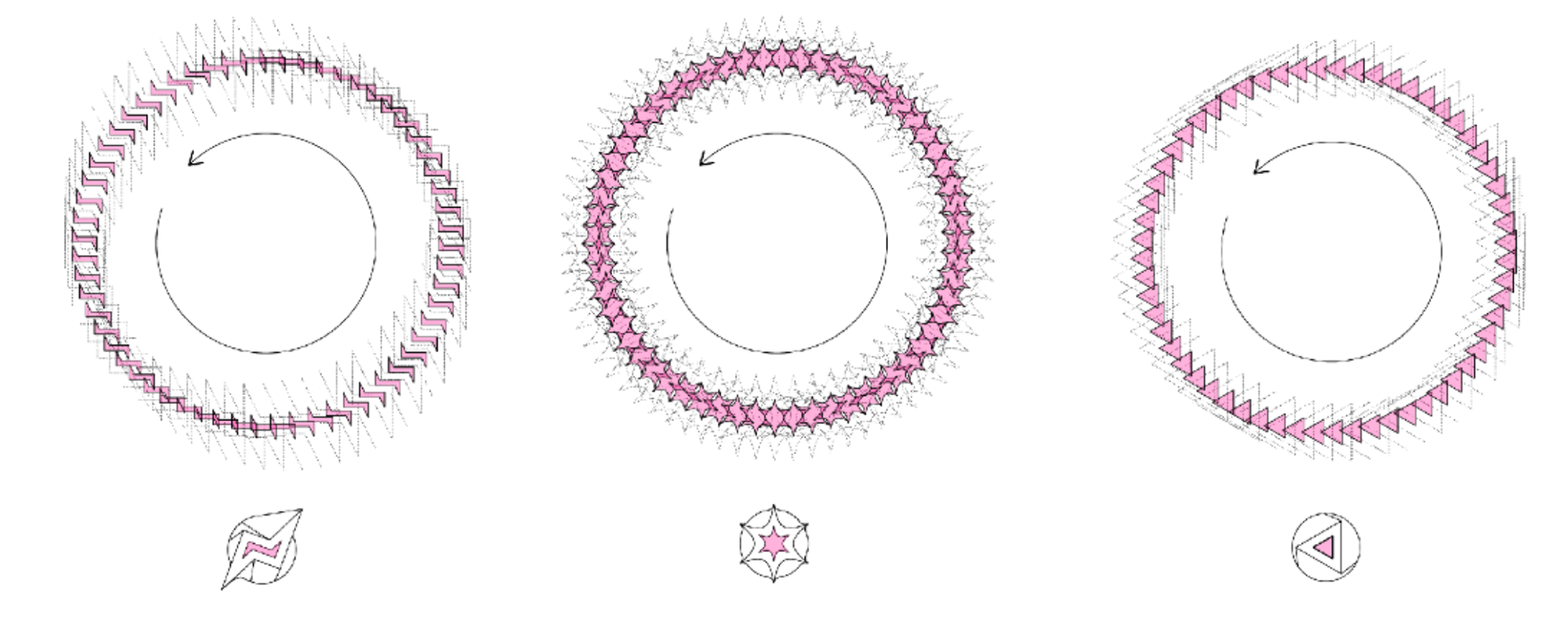
These diagrams indicate the horizontal rotation of the Potterbot bed in plan around the stationary nozzle, creating overlaps and rotations in the geometry as the cylinder is printed. From left to right: 90-degree lightning bolt, 6-sided filleted star, and a 3-sided polygon.
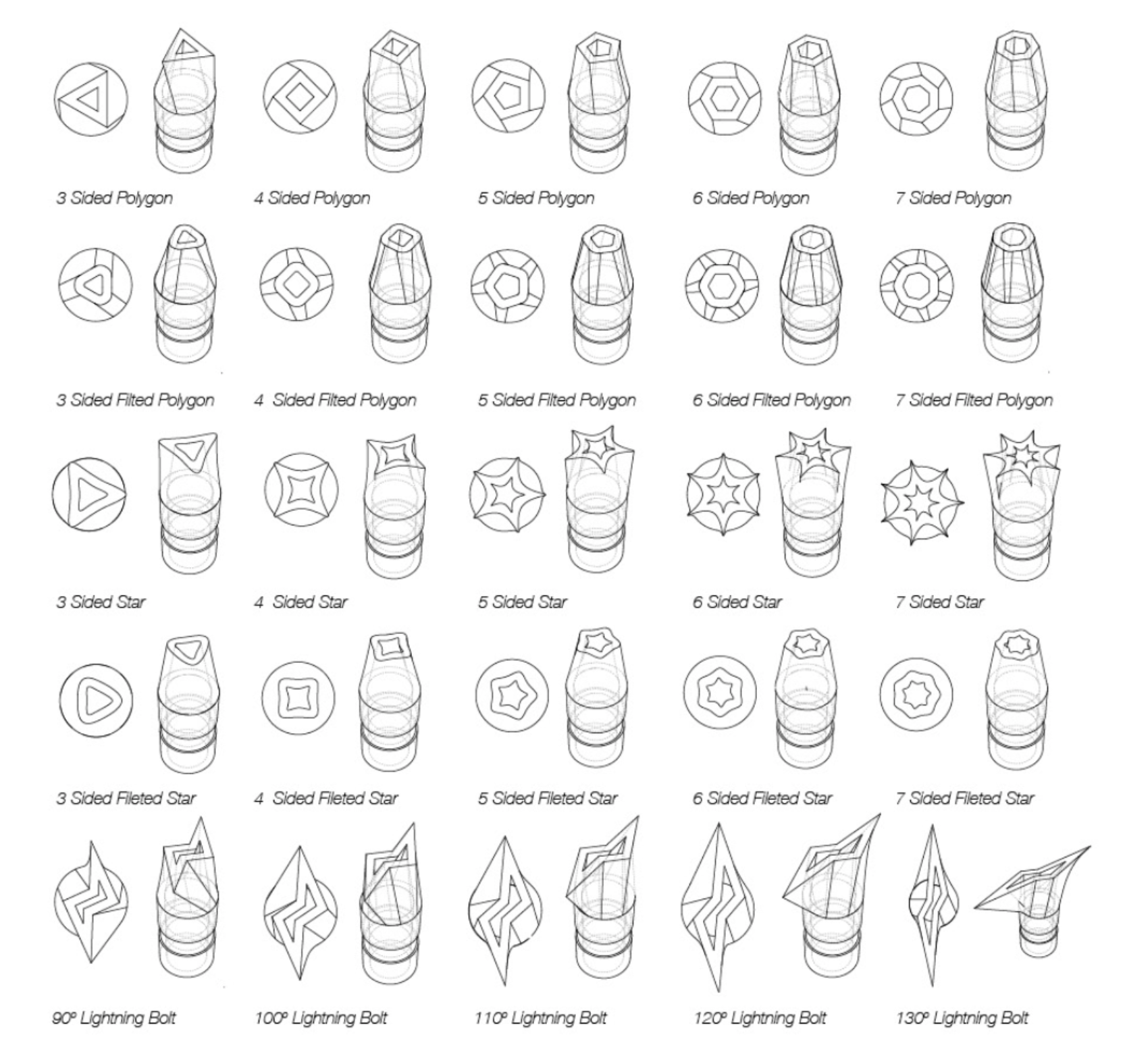
Taxonomy of custom nozzle designs.
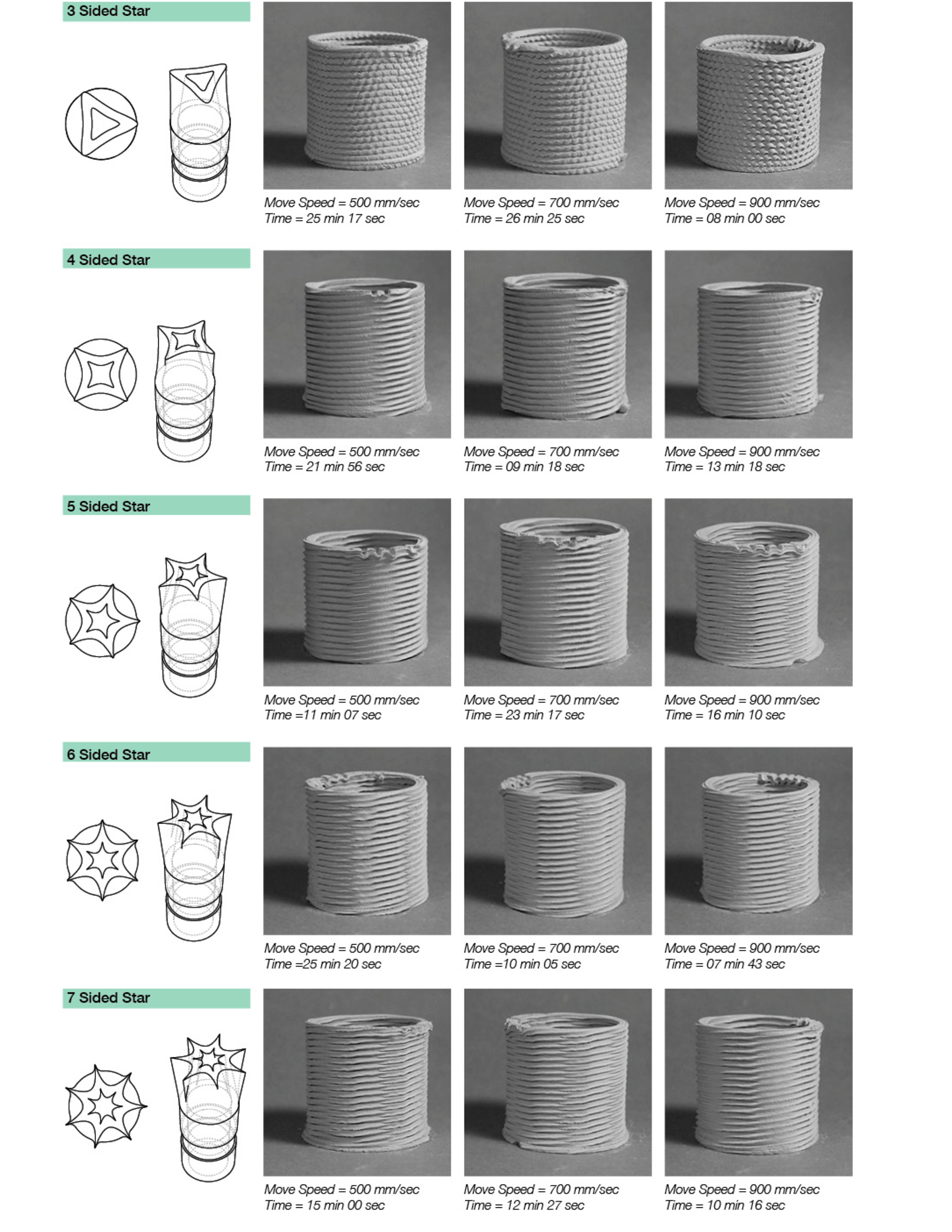
Taxonomy of ‘star’ group of printed nozzles and resulting cylinders
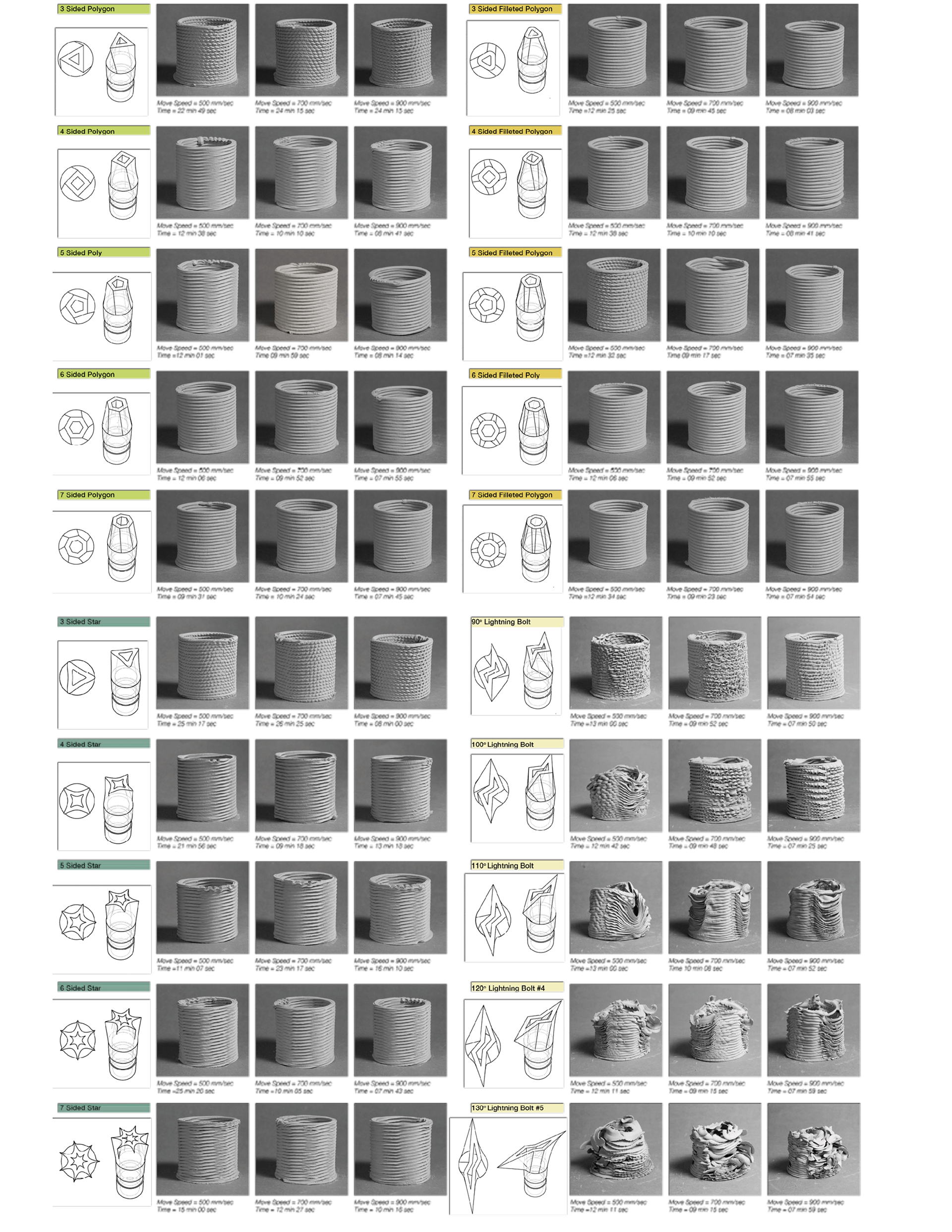