In collaboration with the preserve Iowa Summit Blackbird Investments took part in the design and construction a temporary parklet in a vacant grassy field in Newton, Iowa. The parklet was on display June 6-10, 2019.
Design Team:
James Spiller
Nathan Scott
Drew Petersen
Erin Hunt
James Spiller
Nathan Scott
Drew Petersen
Erin Hunt
Construction Assistance:
Ben Johnson
Ryan Doyle
Katie Taylor
Ben Johnson
Ryan Doyle
Katie Taylor
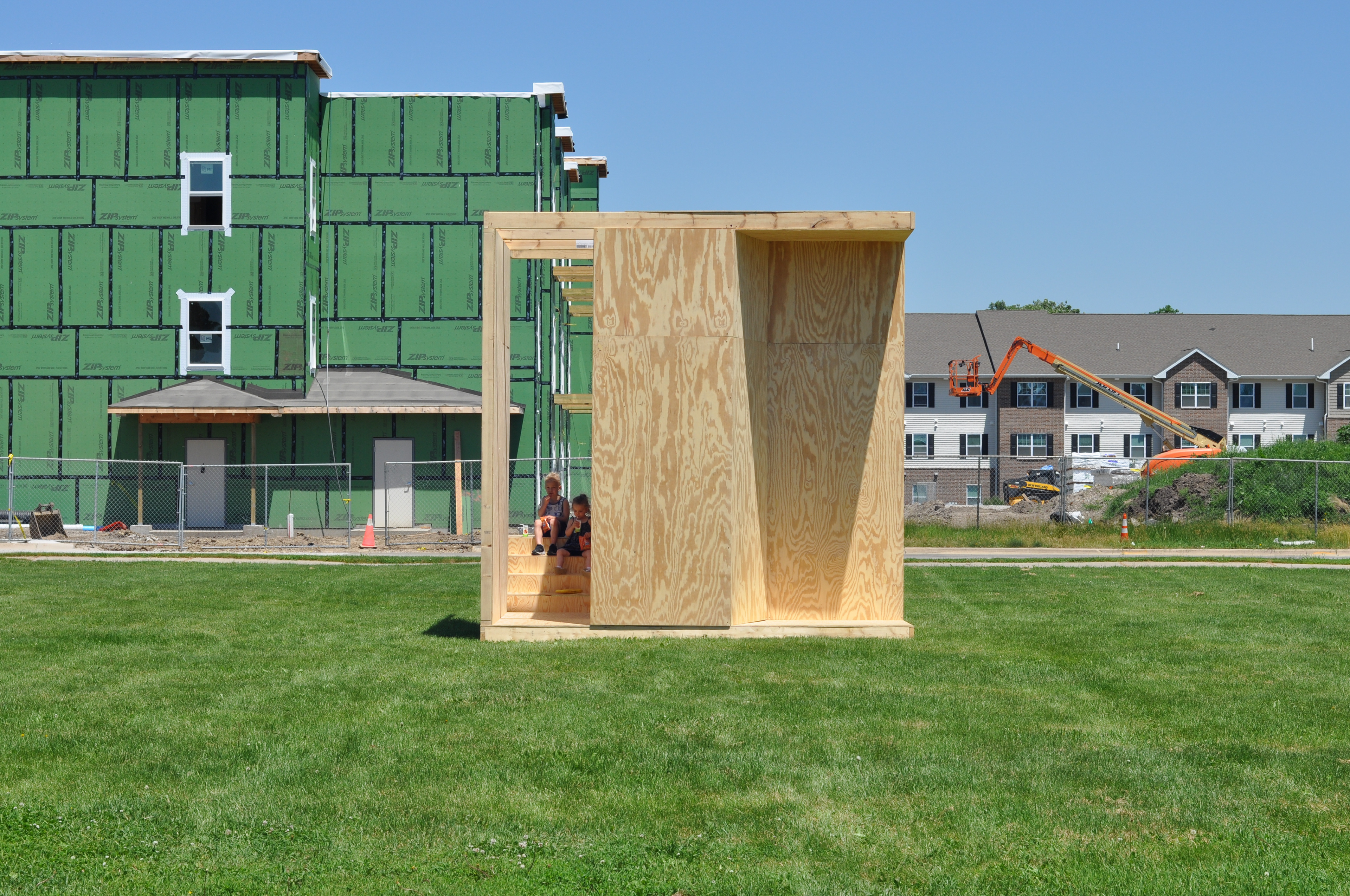
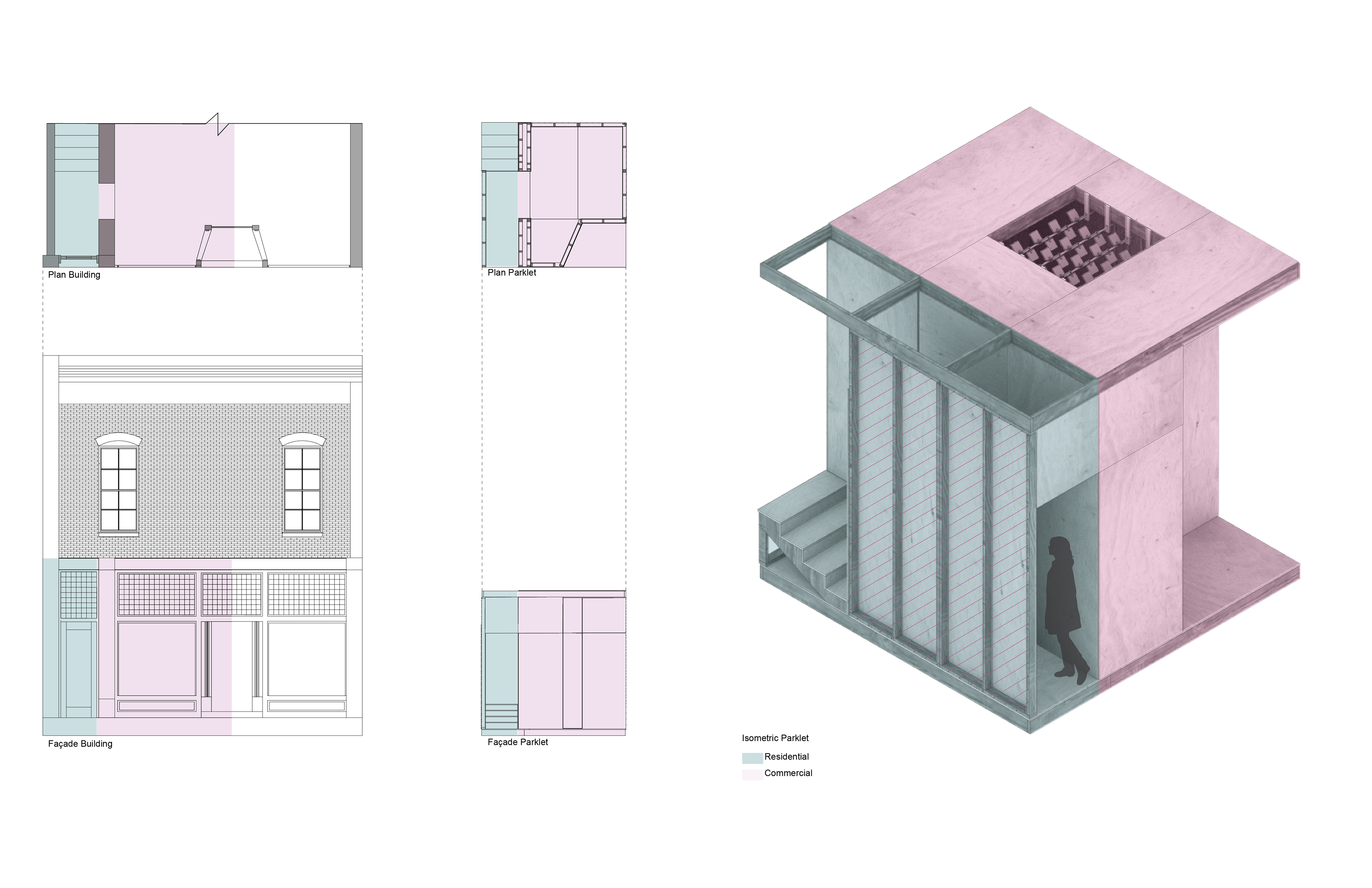
The form was derived by extracting a portion of a common commercial building style of the 19th century. This style consisted of single or double door with window displays on either side. The entrance was set back to allow for protection from inclement weather and to increase the amount of space for displaying merchandise. There was often an additional side door to provide access to the upper residential floors.
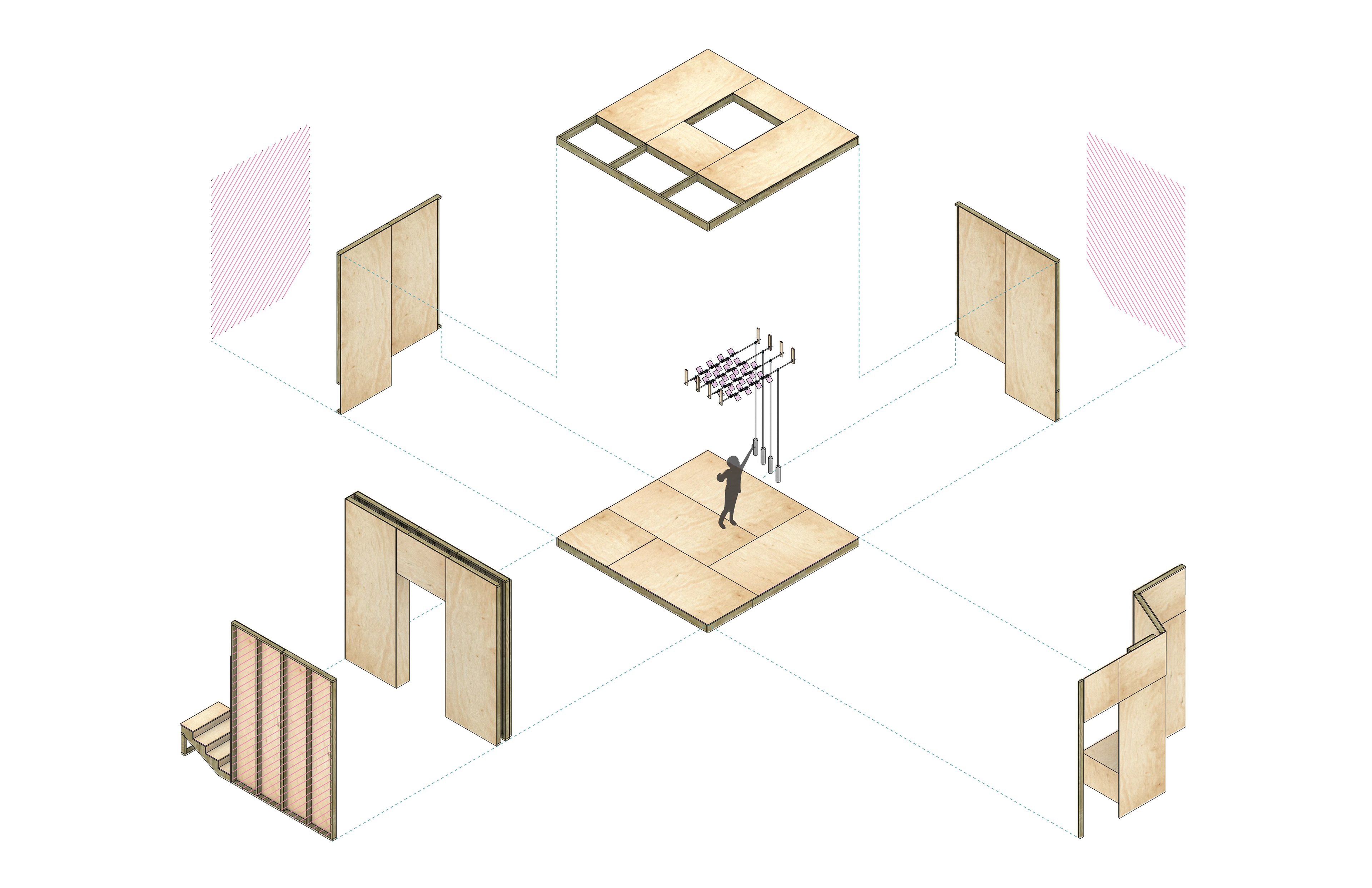
Exploded Isometric
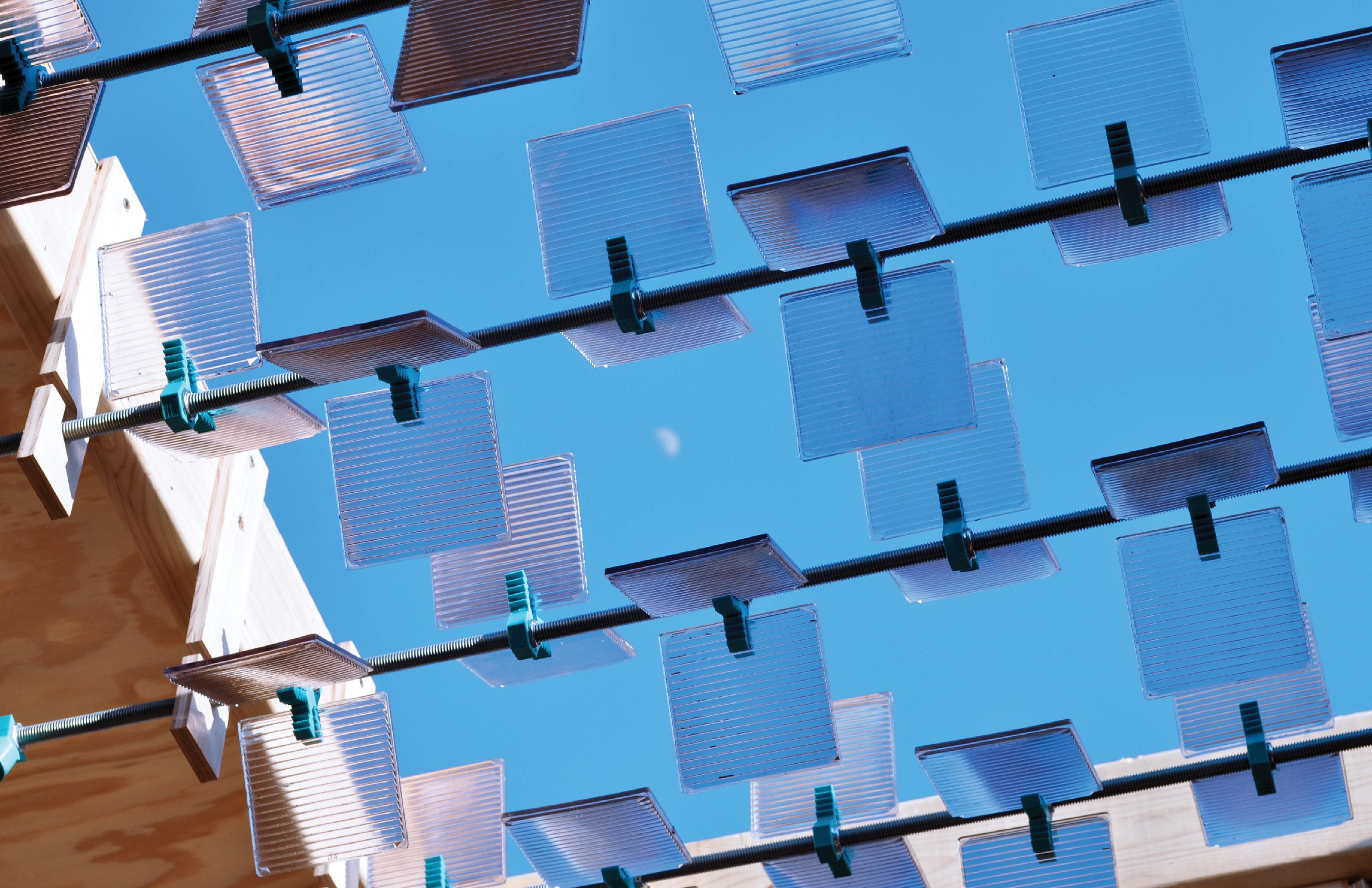
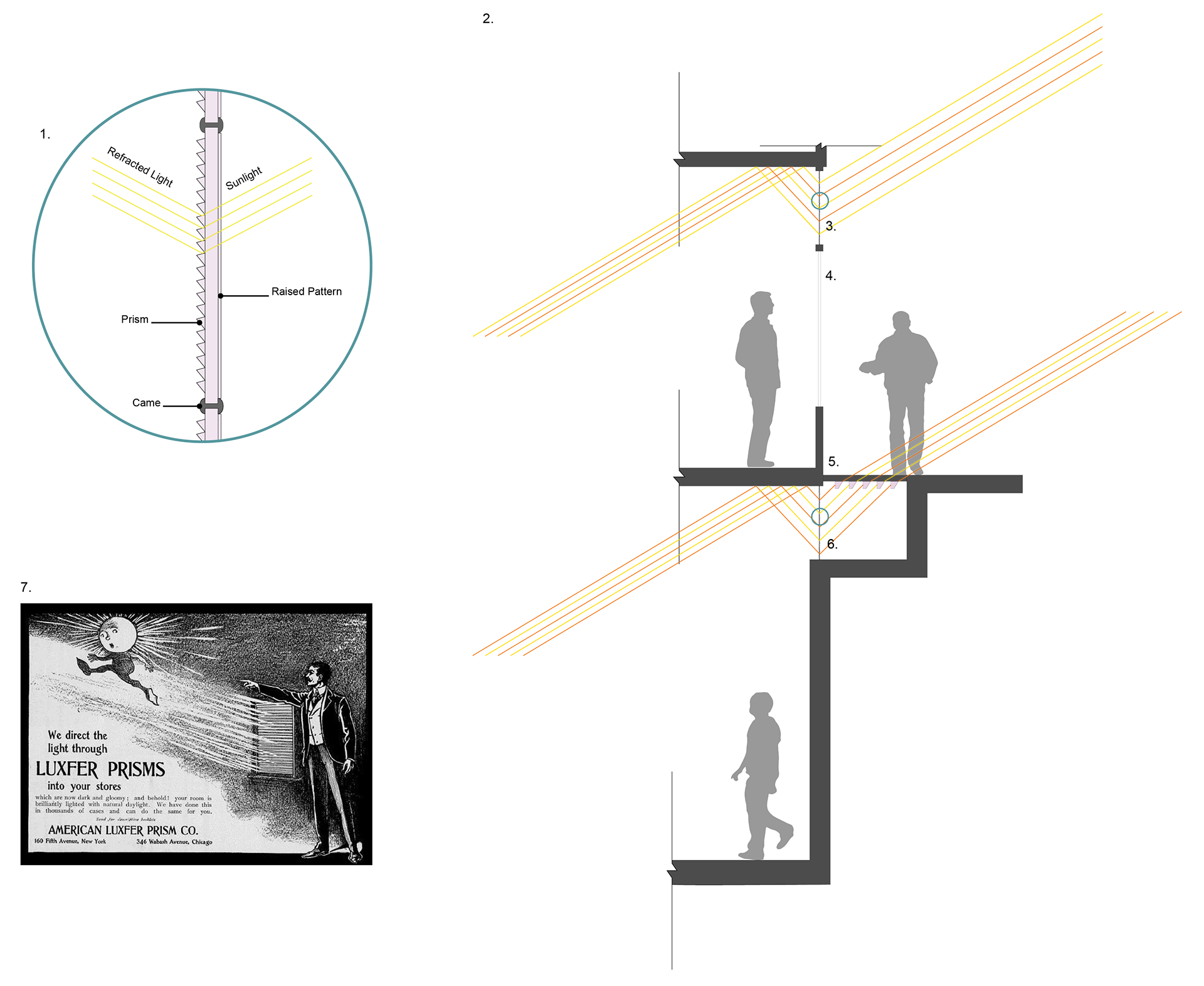
Prismatic glass tiles were used in the late nineteenth and early twentieth centuries prior to the advent and democratization of artificial, electric lighting. The exterior face of Prismatic glass was extruded outward. This outward extrusion captures natural light and carries it through the tile to the interior face of the tile. The interior face of the tile is composed of saw blade extrusions the top face of the tile refracts the light upward toward the ceiling which carries daylight further into the interior space.
1. Call out showing the typical prism glass connection.
2. A section displaying typical installations of prism glass.
3. 9 x 9 grid of prism tiles in a transom. This arrangement allowed for daylight to permeate the back of the store.
4. Glass Display Window
5. Prism glass blocks were integrated into iron grates and cast in concrete to provide natural light to a building’s basement.
6. 9 x 9 grid of prism glass to refract the daylight into the space.
7. Advertisement encouraging businesses to use Luxfer Prism Glass Tiles.
2. A section displaying typical installations of prism glass.
3. 9 x 9 grid of prism tiles in a transom. This arrangement allowed for daylight to permeate the back of the store.
4. Glass Display Window
5. Prism glass blocks were integrated into iron grates and cast in concrete to provide natural light to a building’s basement.
6. 9 x 9 grid of prism glass to refract the daylight into the space.
7. Advertisement encouraging businesses to use Luxfer Prism Glass Tiles.
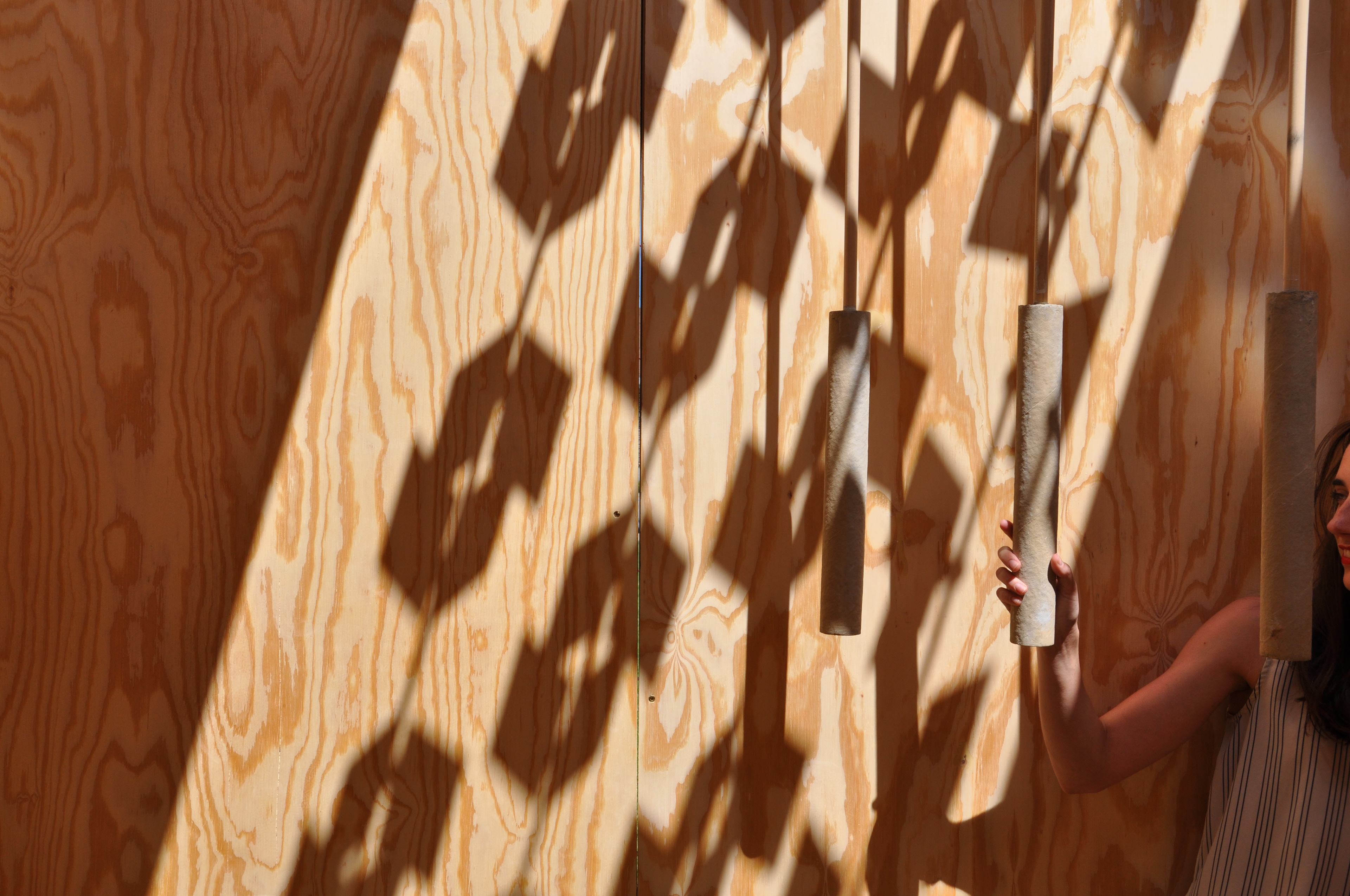
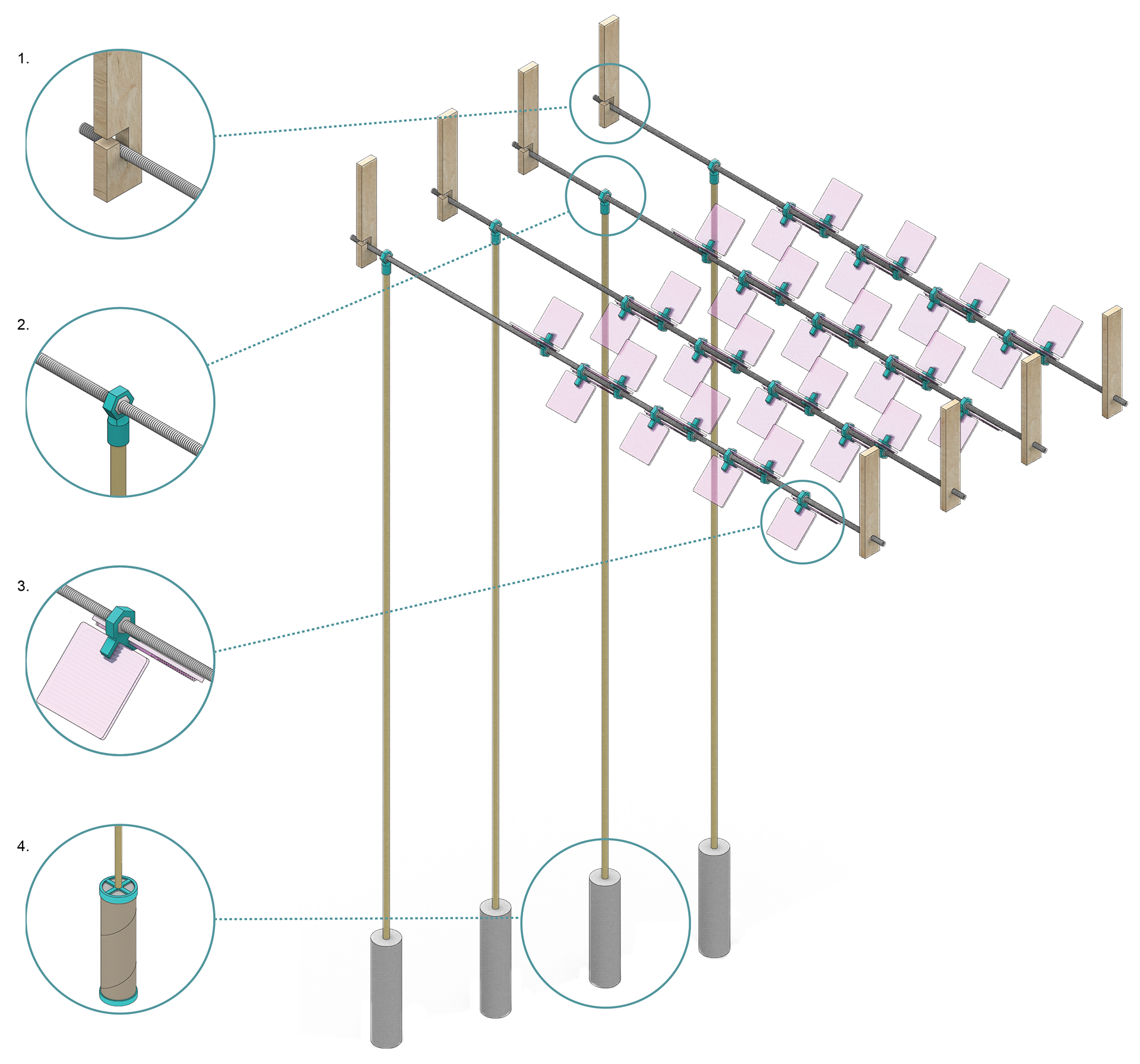
Eighty, four by four inch prismatic tiles salvaged from a building’s transom and used to create a chandelier in the center of the parklet. This was created as a reminder that when you peal away the layers from a boarded up façade there are beautiful, forgotten elements.
1. A computer numerically controlled (CNC) router was used to create custom holders for the spanning threaded rods.
2. Custom 3D printed, teal connections were made to both hold a popular dowel rod and a 1/2” lock nut. This allowed the threaded rods to be rotated which allowed the users to alter the orientation of the tiles and in turn the shadows and refraction.
3. The prism tiles were slide into two types of 3D printed joints. These tiles were held on the threaded rod with 1/2” lock nuts which kept the tiles from moving.
4. The dowel rods were cast in concrete to add both a handle and weight. The dowels' handles were cast in two-inch diameter paper tubes. A 3D printed base and top were used to hold the dowel at the center of the tube. The apertures in the top cap were to allow the concrete to enter the mold.
2. Custom 3D printed, teal connections were made to both hold a popular dowel rod and a 1/2” lock nut. This allowed the threaded rods to be rotated which allowed the users to alter the orientation of the tiles and in turn the shadows and refraction.
3. The prism tiles were slide into two types of 3D printed joints. These tiles were held on the threaded rod with 1/2” lock nuts which kept the tiles from moving.
4. The dowel rods were cast in concrete to add both a handle and weight. The dowels' handles were cast in two-inch diameter paper tubes. A 3D printed base and top were used to hold the dowel at the center of the tube. The apertures in the top cap were to allow the concrete to enter the mold.
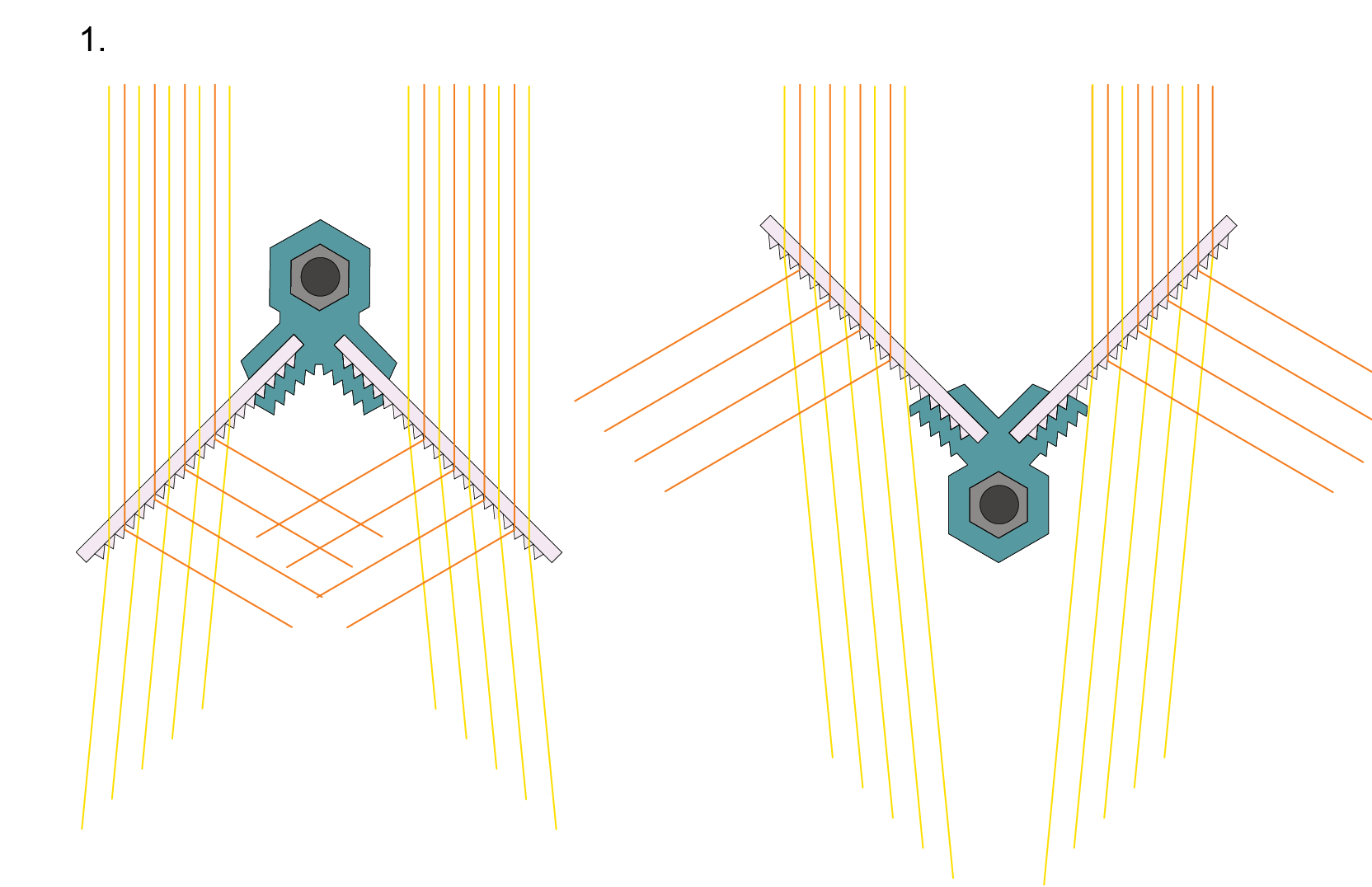
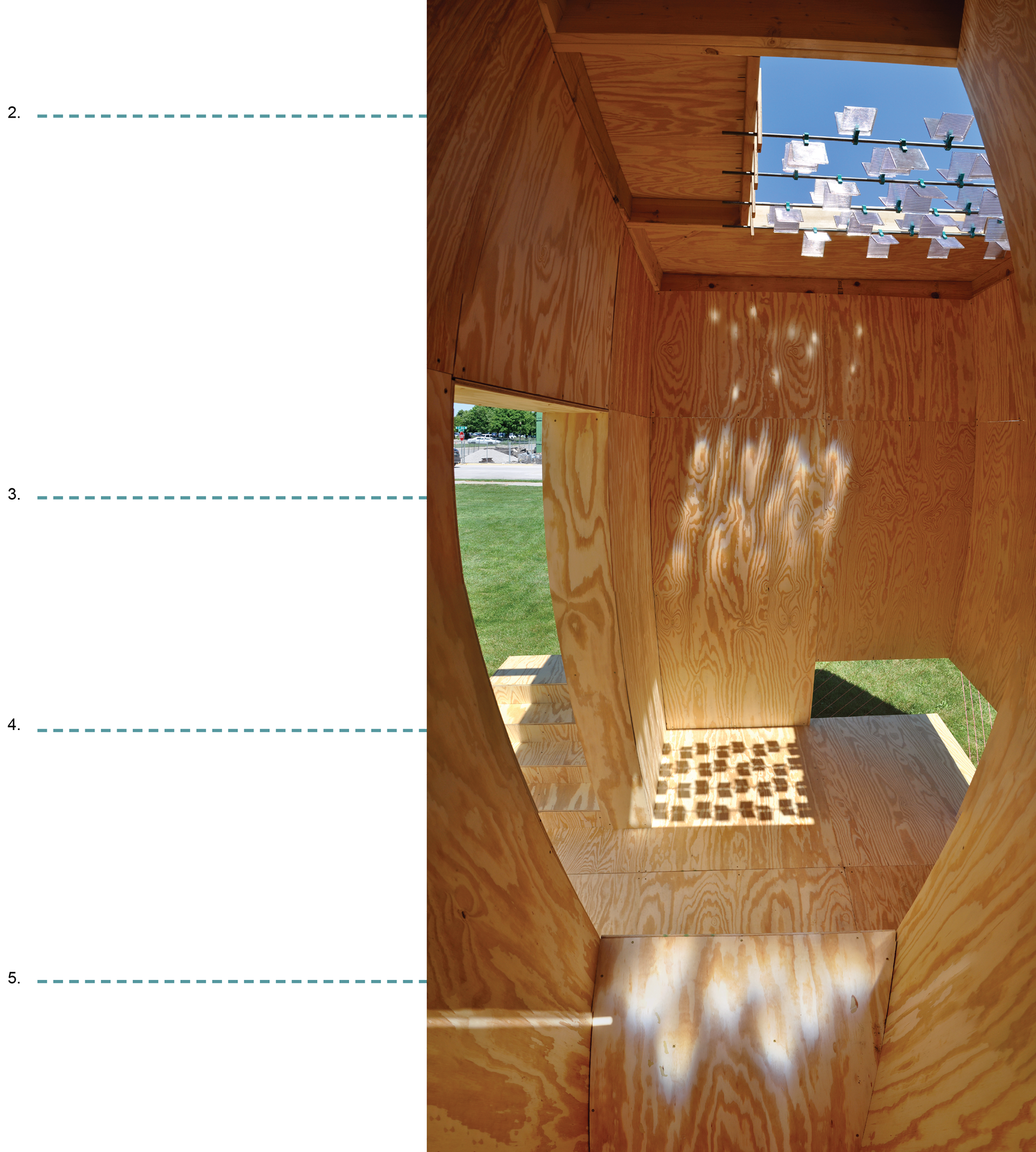
The interior lighting quality was most engaging from 10 AM to 2 PM. During this period there were a series of lighting conditions resulting from the daylight hitting the prism glass tiles. As a result of the 90 degree angle orientation of the tiles the light reactions were mirrored to either side of the parklet’s interior.
1. The tiles were placed in two orientations. In both configurations, the tiles were separated by 90 degrees. The extruded side was consistently upward to catch the light. This created the need for two connections to accommodate the saw tooth sides of the tiles. The tolerance of the connection was tight enough that the tiles did not move laterally without a substantial about of force. The angle of the tiles allowed for refraction on either side of the parklet’s interior. The light was refracted in two directions from each tile.
2. Prism Glass Chandelier
3. Light refracting off the prism tiles.
4. Chandelier’s shadow cast onto the floor of the parklet.
5. Light refracting off the prism tiles.
2. Prism Glass Chandelier
3. Light refracting off the prism tiles.
4. Chandelier’s shadow cast onto the floor of the parklet.
5. Light refracting off the prism tiles.
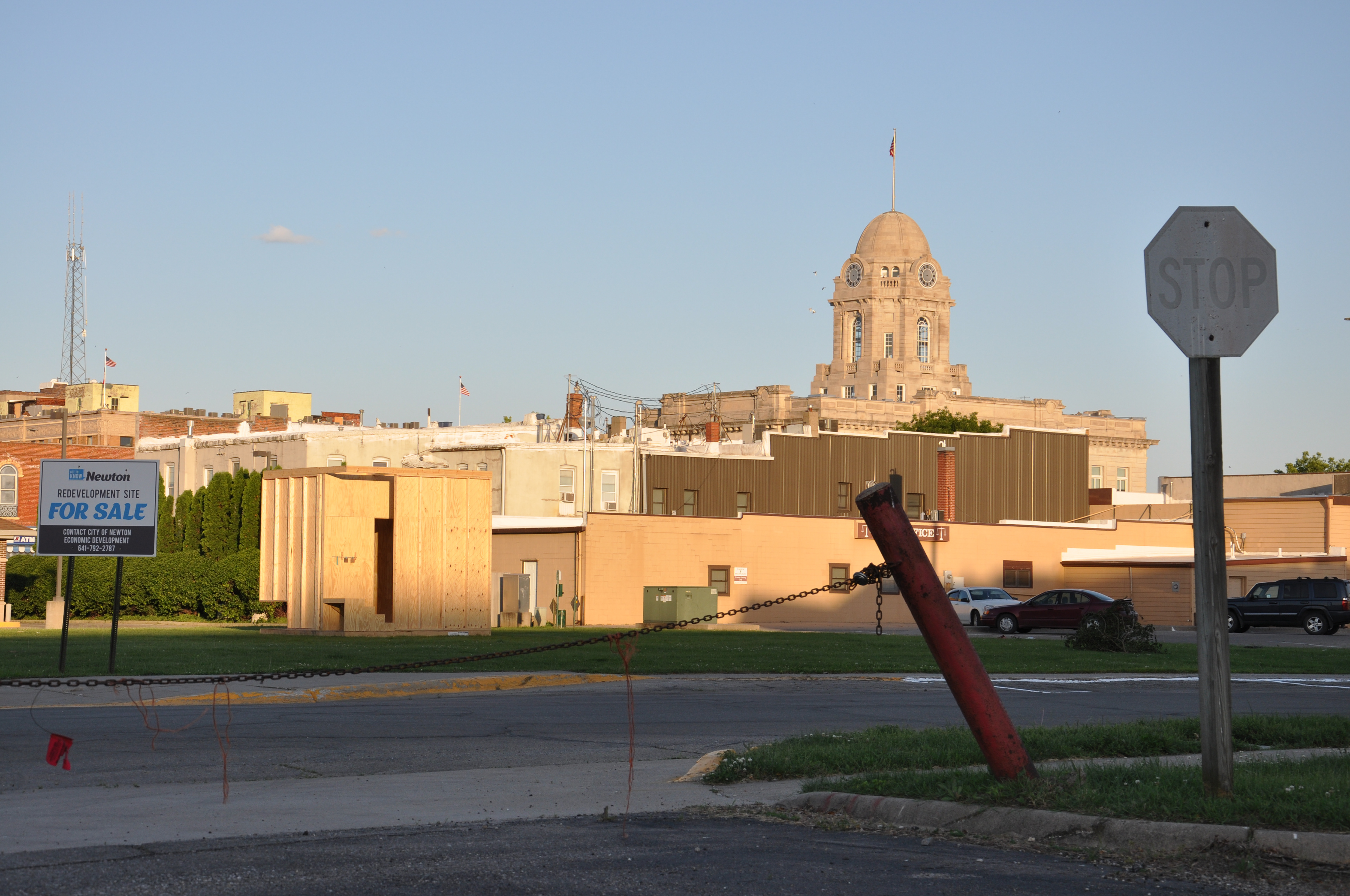
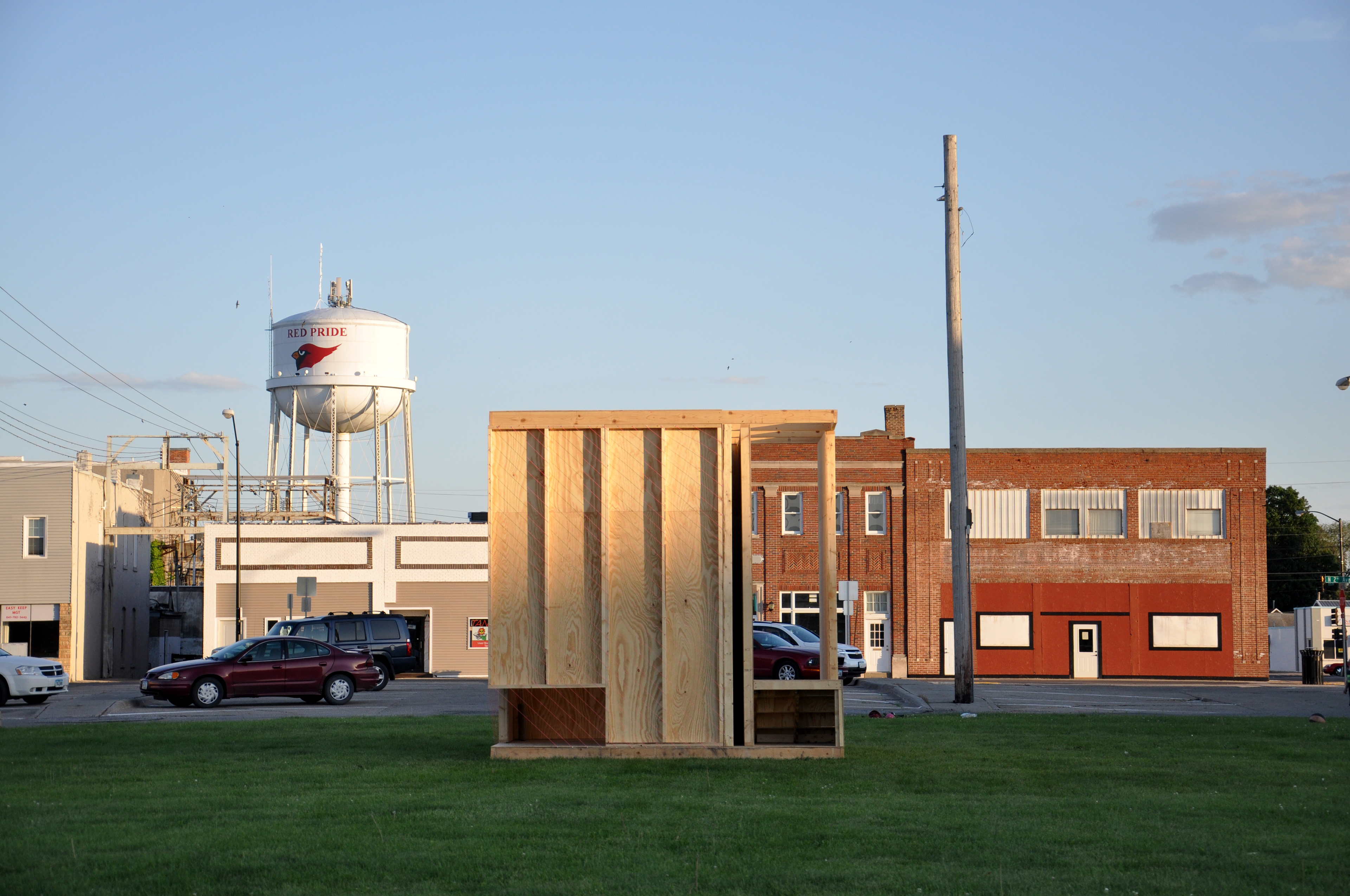