Advised by Jonathan Grinham, DDes
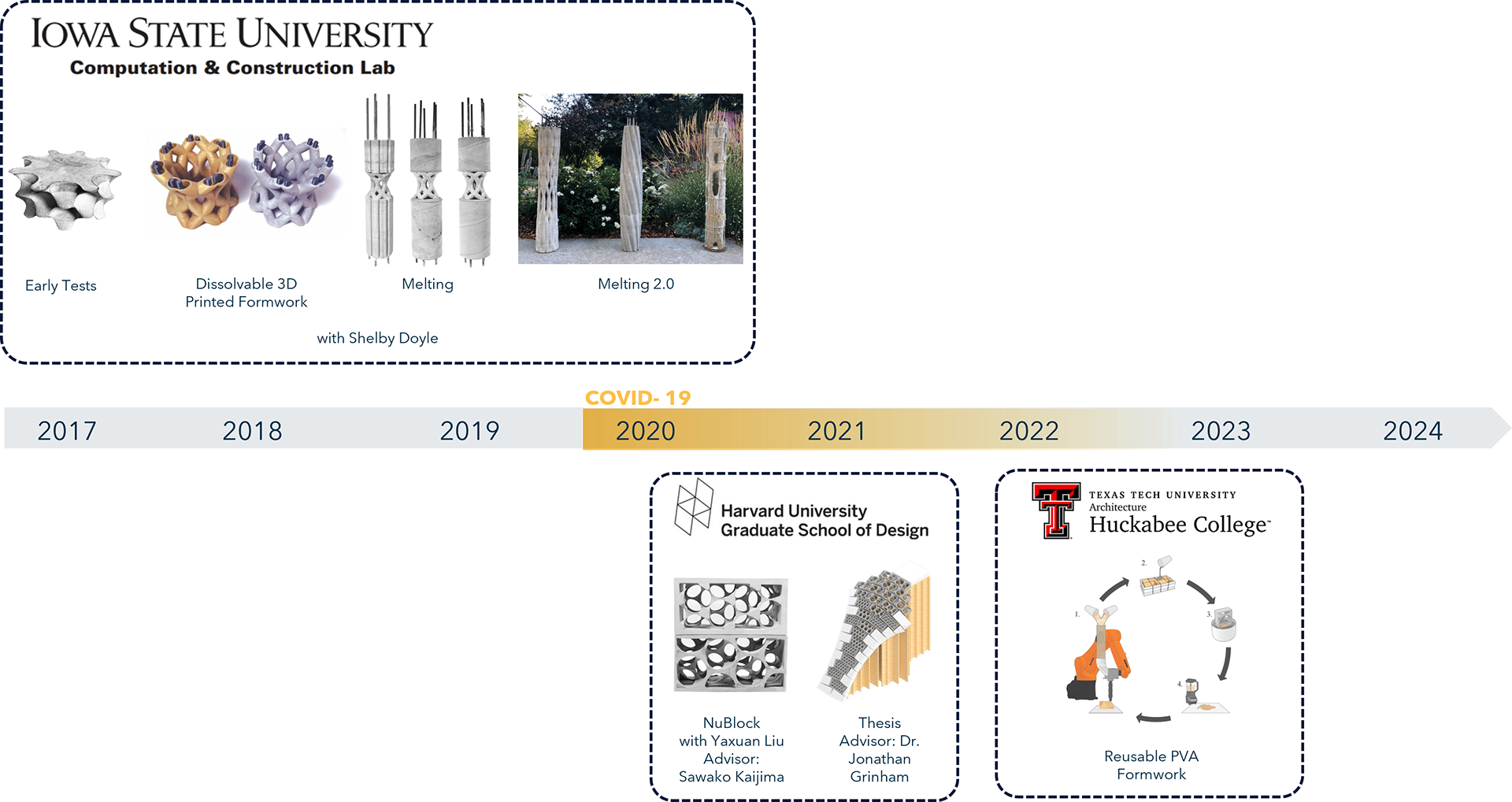
This work focuses on using water-soluble Polyvinyl alcohol, or PVA, as the primary material for 3D-printed formwork. This material allows for a straightforward removal process and the creation of novel geometries that could not be fabricated using traditional methods. PVA formwork enables concrete components with hollow parts, undercuts, and other scenarios where removing or breaking the formwork by hand or with machines would be impossible. Past related research I conducted with Shelby Doyle at Iowa State University applied PVA formwork to fabricate multiple columns that introduced moments of geometric complexity using PVA formwork in conjunction with traditional formwork methods such as Sonotubes. This paper introduces work explored during my master's thesis at Harvard Graduate School of Design and ongoing research conducted as a faculty member at Texas Tech University’s Huckabee College of Architecture. It explores the opportunities of PVA as a reusable, water-soluble 3D printed formwork for a more circular and complex concrete casting. This presentation will first explore the feasibility of reusing PVA by discussing the various methods of expediting its dissolution process, harvesting, and dehydrating the material for recycling. Next, a partial vault structure fabrication case study will be introduced to explore material optimization enabled by water-soluble 3D printed formwork and finite element analysis methods. A series of block designs were compression tested, demonstrating that the integration of reinforcement and certain design choices were effective.
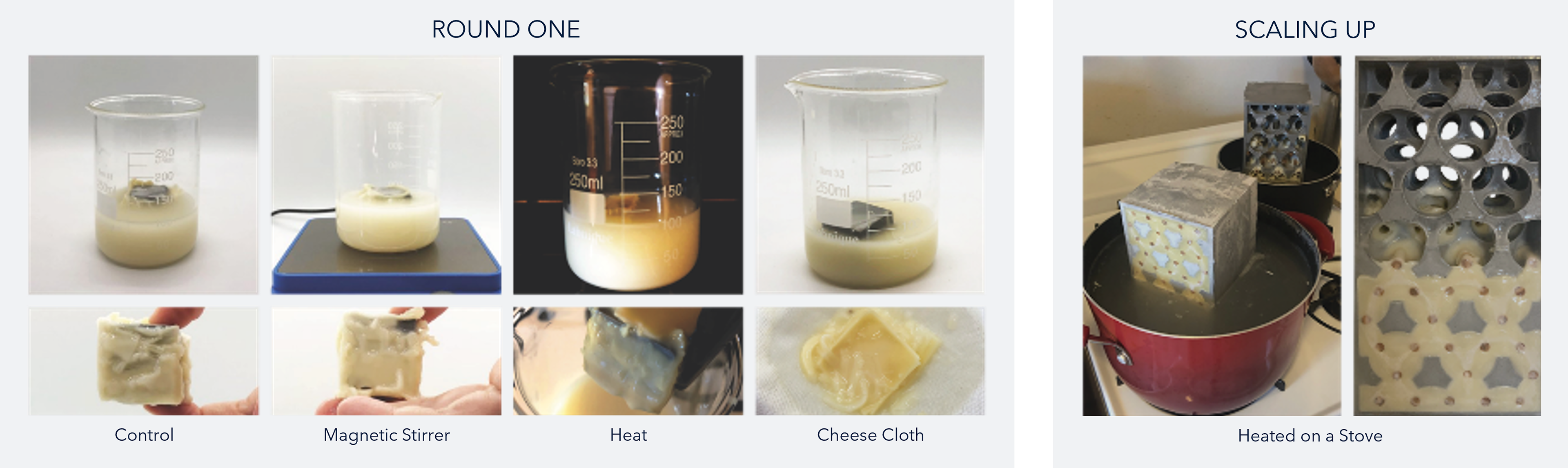
Initial research explored methods for expediting PVA dissolution. A formwork was designed with a 2 mm offset of PVA to create 16 cubic millimeters of Rockite. Due to the PVA’s buoyancy, the Rockite was used to better simulate the surface area exposed to water and allow for full PVA submersion. Five tests were used to examine various dissolution methods to determine which is most successful regarding the time it takes to dissolve the PVA. Tests using the same amount of water under different conditions were conducted. The tests included a control using room temperature water, agitation, heat from placement in an oven, and straining the mixture with cheesecloth. Placement of the mixture into the oven proved most successful in expediting the process. Through this test, it was realized that PVA remained post-dissolution. As the scale of the cast increased, tall pots on a stove were used to heat the water. As a result of the increased heat from the stove, the process was further expedited to one hour per block—the increased size allowed for multiple block formworks to be dissolved simultaneously. It was determined that approximately 95 degrees Celsius is optimal.
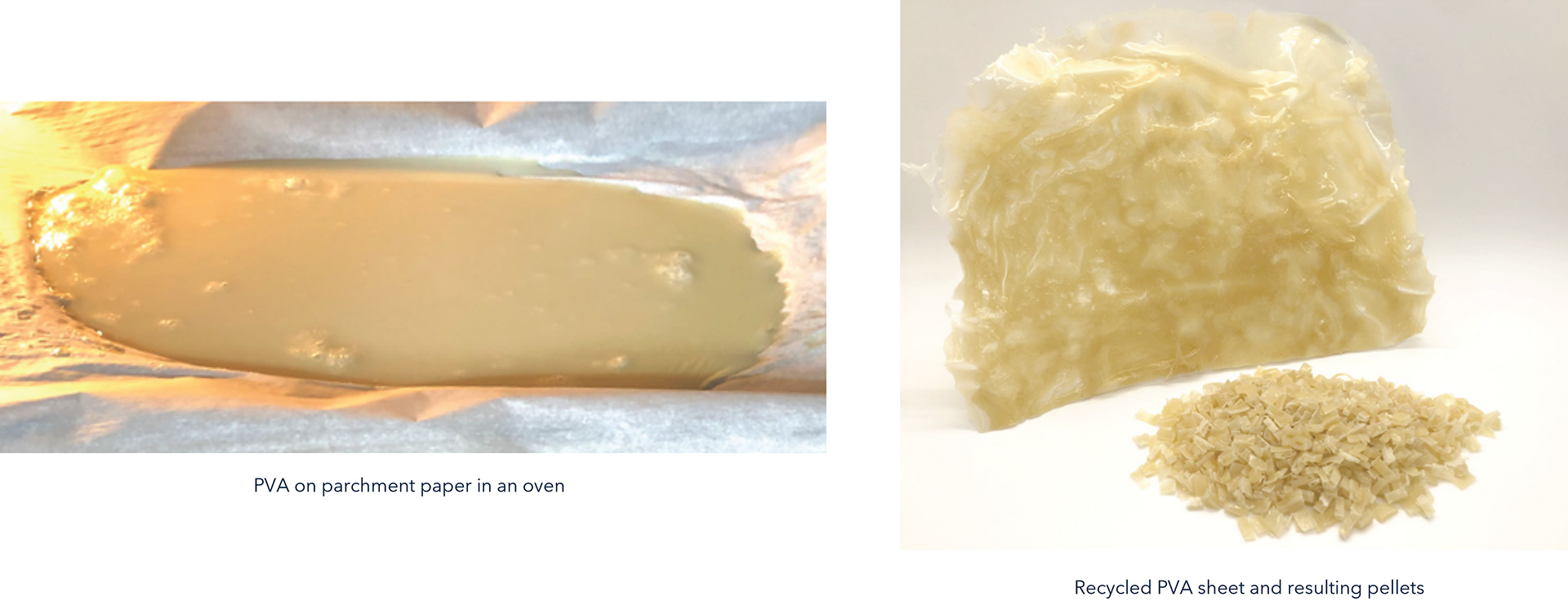
While conducting the dissolution test, it became apparent that the PVA can be conserved through dehydration. The average material conservation rate was 70%. The PVA and the water remain heated after the casts are removed to further reduce the water content before being transferred onto parchment paper and a sheet tray. The sheet tray is then placed into an oven at 170 degrees Celsius to remove any excess water from the PVA. Once dehydrated, the sheets are cut into pellets.
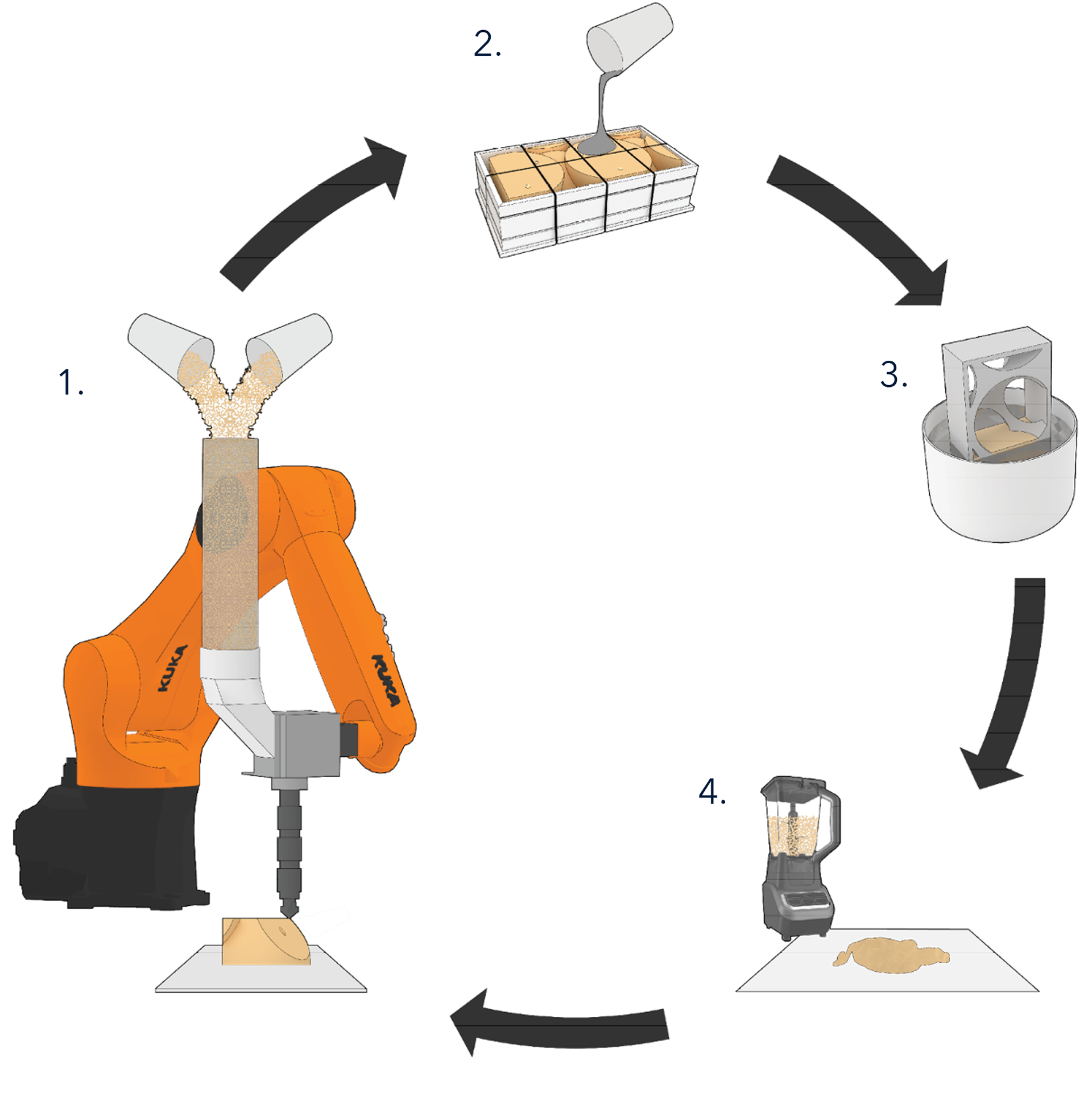
This diagram depicts the reuse cycle. Beginning with 3D printing and moving through the casting, dissolution, and dehydration process. It was found that a blender could be used to chop the filament into pellets. Soon, we will have an industrial grinder to expedite the processes further. This recycled filament can be directly printed with a pellet extruder using a robotic arm.
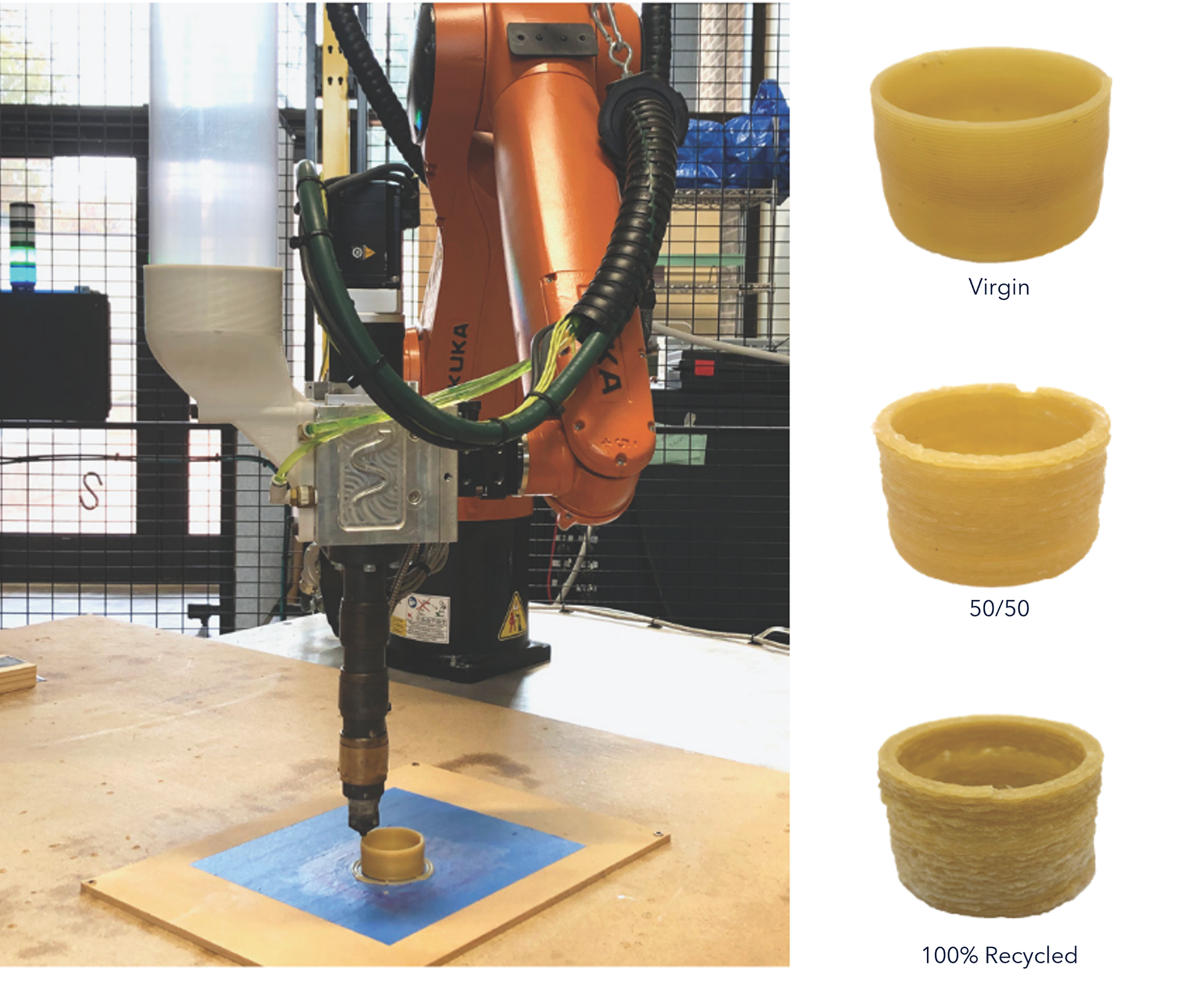
A pellet extruder was used on a KUKA KR10 robotic arm to test the viability of reusing the PVA. The initial tests printed a cylinder with a 50 mm diameter using virgin PVA to determine the proper extrusion, temperature, and movement settings. The most successful settings were 350 rotations per minute for extrusion, an extruder temperature of 175˚C, and a 10 mm/s move speed. The material was printed on painter’s tape with a layer of PVA glue stick applied for part adhesion. The second test utilized 50% virgin and recycled PVA pellets. The final test employed solely recycled material. There was a slight increase in weight of 2 grams with the 50% and 3 grams when the 100% recycled pellets were used. The bead width increased by 1.25 mm. The diameter increased by 1 mm. Additional testing must be conducted to determine if and how often the material can be reused. Future research must include mechanical testing of the recycled material prints.
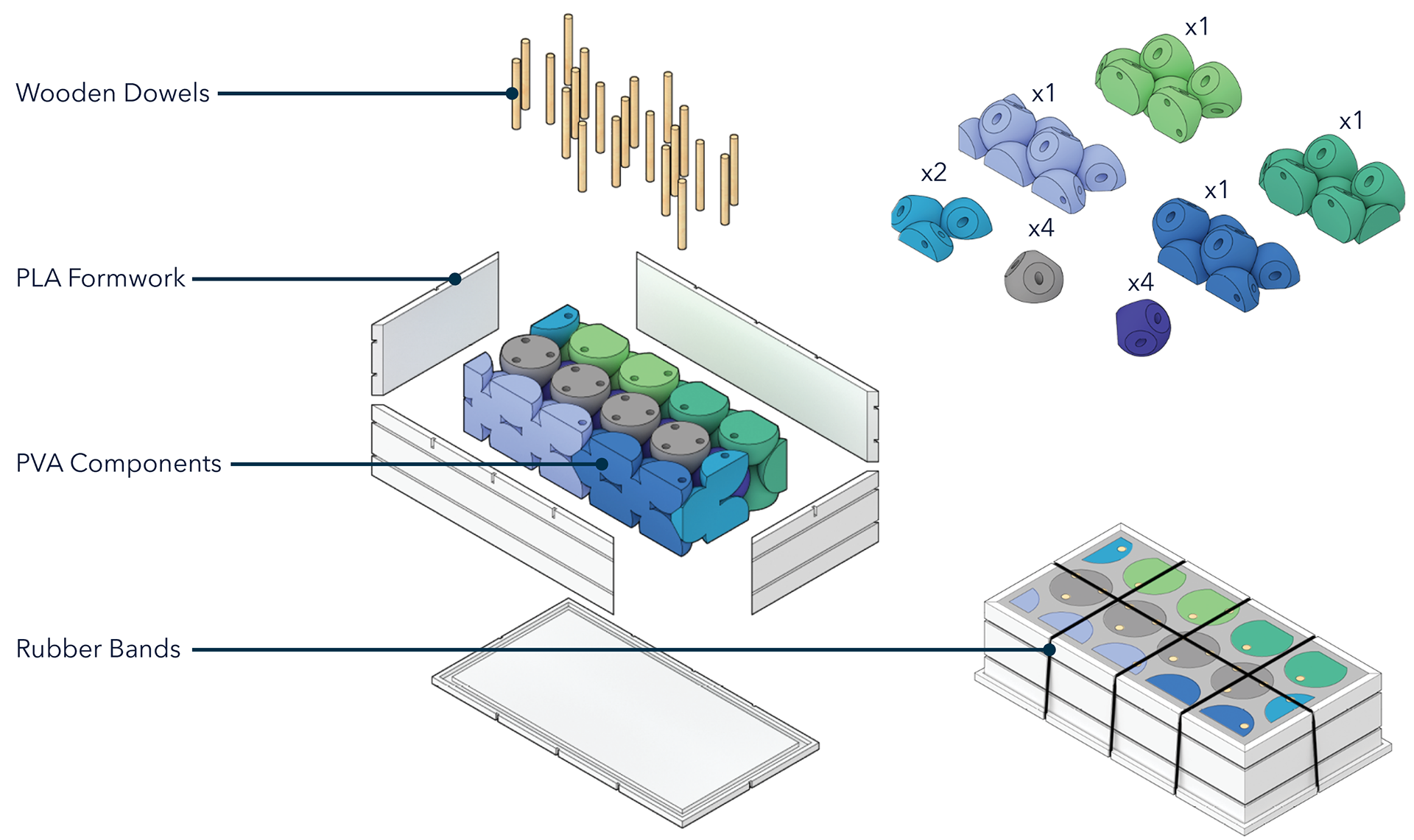
A novel formwork method was developed for this project since the 3D printer used had a limited build volume of 160 x 160 x 180 mm. The PVA was printed in multiple parts that could be held together with a 5 mm diameter wooden dowel rod. The new strategy of dividing the formwork into multiple parts allowed for the elimination of 3D-printed support structures since there was no material bridging. This aggregation of PVA parts allowed the block’s volume to increase beyond the confines of the printer’s volume. An additional formwork was created to complement the PVA. The second, reusable formwork was printed in Polylactic Acid (PLA) filament. The PVA was attached with a water-soluble glue. This formwork was designed to be reused for each block.
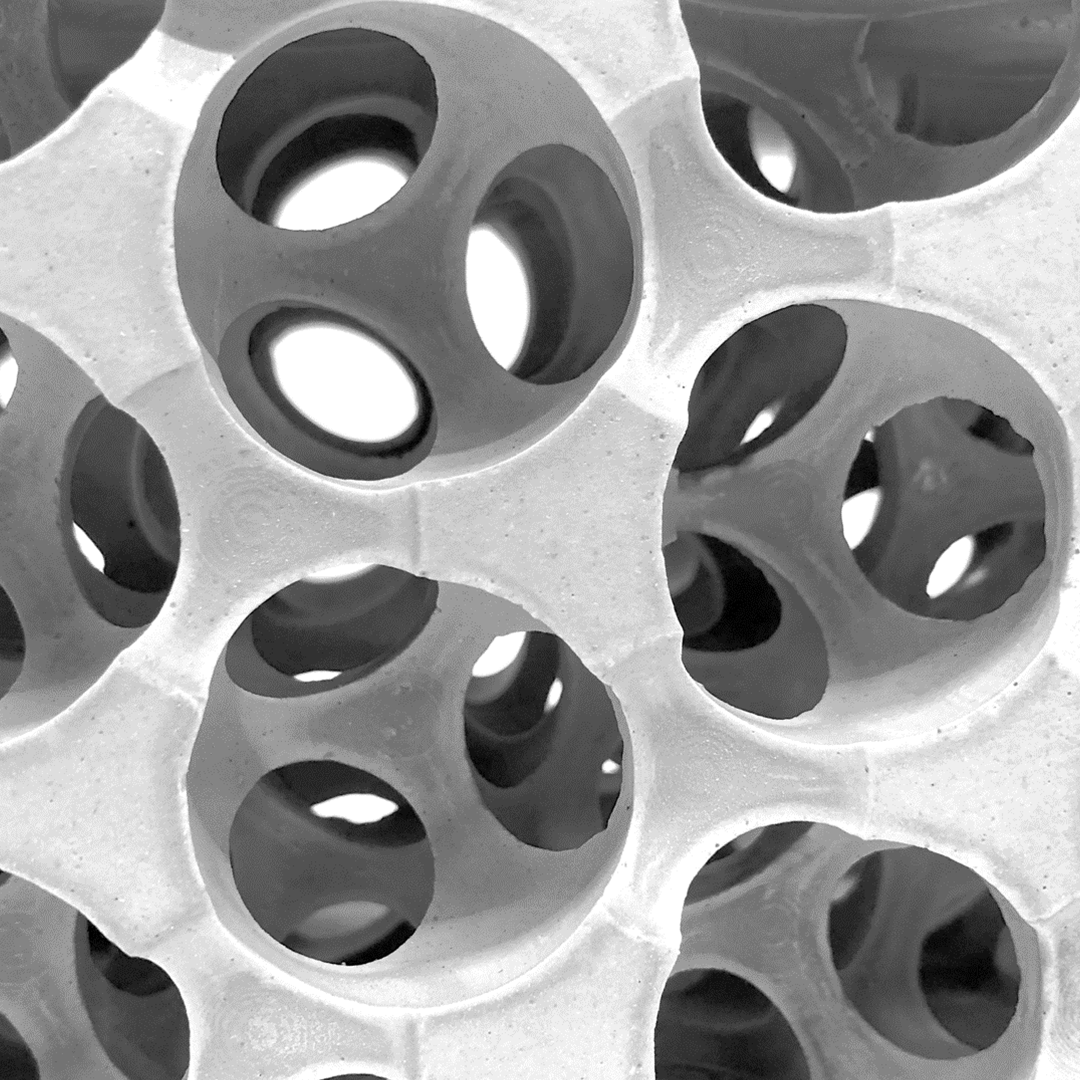
At left is a GIF of the formwork being constructed with wooden dowels. At right shows a detail shot of the densest design depicting the complexity and detail that can be achieved with this fabrication method.
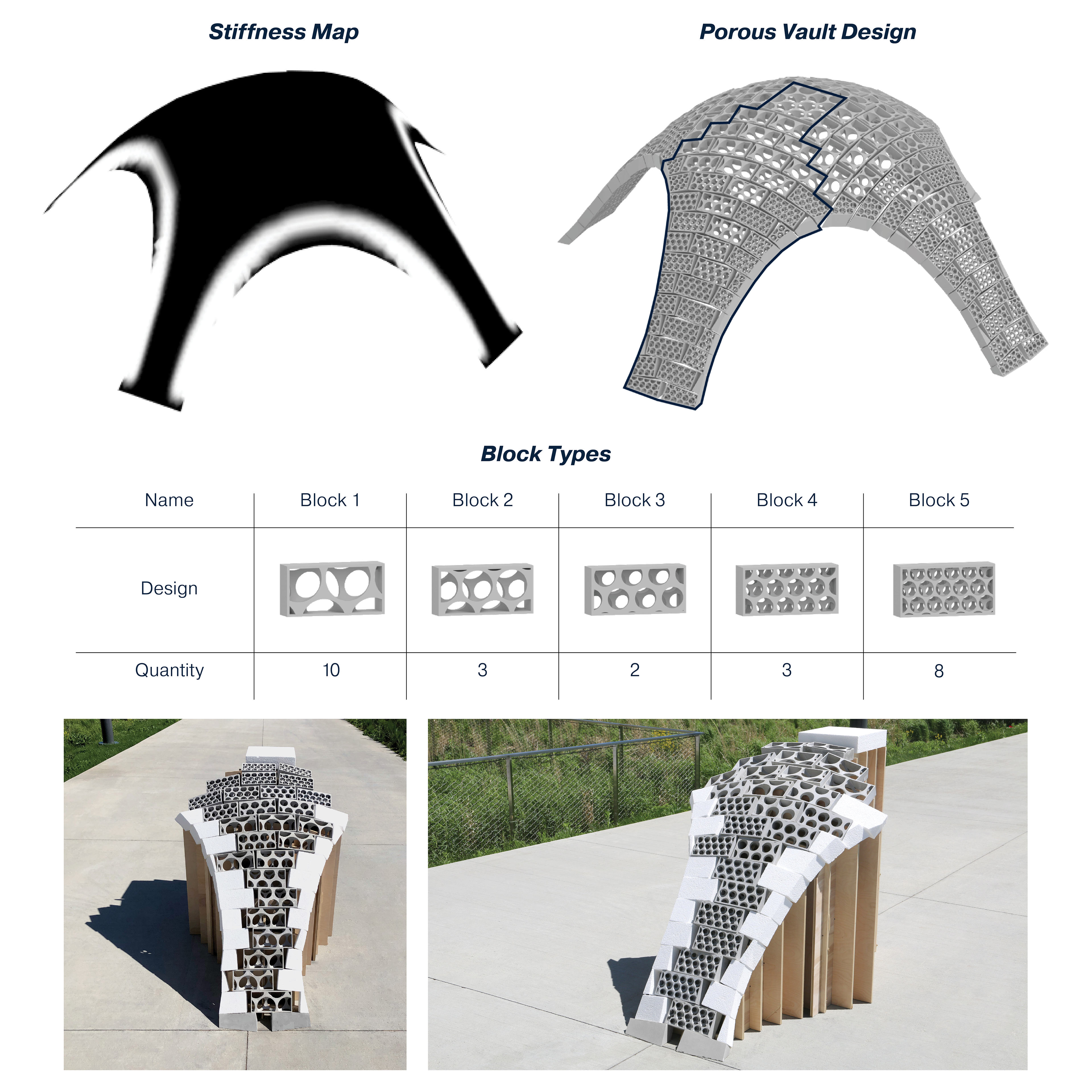
A quarter section of the vault was fabricated to test this fabrication method's viability. Its bounding dimensions were 1 x 1.5 x 1 meters.
The brick design was based on hexagonal sphere packing. The cell size determined the density of the spheres, which allowed for varying porosities and structural strength. The spheres were used to remove material from a block. An exterior boundary remained on four sides to make the module more legible once populated on a structure. Five brick types were designed with a gradient of porosity. The shell model analyzed an optimized Catalan vault with its self-weight. By draping a chamfered square, RhinoVAULT generated the geometry and produced the most effective structure. A stiffness map of the surface was created using Millipede, a Grasshopper plugin focused on Finite Element Analysis. A grid was populated onto the surface and used to sample the UV tangents and the stiffness map’s brightness. This was utilized to determine the block orientation and type. This data mapped The blocks onto the surface, so their centroids were at the corresponding grid points.
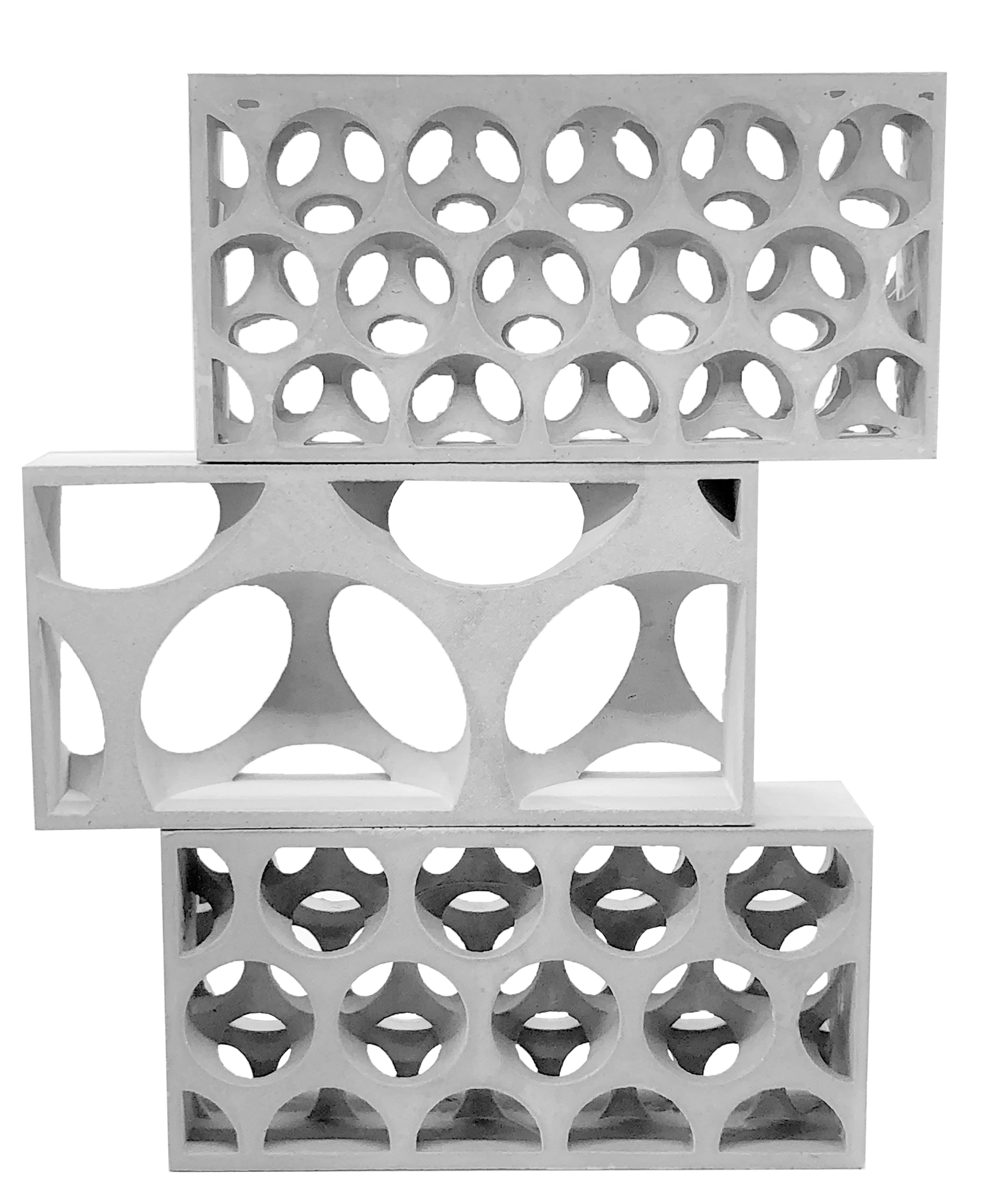